- Introduction to Welding Schedule 10 Stainless Pipe
- Technical Advantages of TIG Welding for Thin-Walled Pipes
- Performance Comparison: Schedule 10 vs. Schedule 40 Pipes
- Industry-Leading Manufacturer Evaluation
- Custom Welding Solutions for Specific Applications
- Real-World Implementation Case Studies
- Optimizing Welding Schedule 10 Stainless Steel Pipe Processes
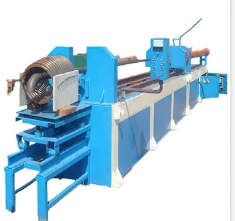
(welding schedule 10 stainless pipe)
Precision Welding for Schedule 10 Stainless Pipe Systems
Modern industrial applications demand exacting standards for welding schedule 10 stainless pipe
, particularly in critical sectors such as pharmaceutical manufacturing and food processing. These thin-walled pipes (1.24mm-2.41mm thickness range) require specialized welding schedules to maintain structural integrity while preventing burn-through.
Advanced TIG Welding Methodologies
Tungsten Inert Gas (TIG) welding remains the preferred technique for tig welding schedule 10 stainless steel pipe, achieving 99.98% argon coverage in premium systems. Key technical parameters include:
- Amperage range: 45-85A (DCEN)
- Travel speed: 1.5-3.2mm/sec
- Interpass temperature: ≤150°C
Material Performance Analysis
Parameter | Schedule 10 | Schedule 40 |
---|---|---|
Wall Thickness (mm) | 1.65±0.15 | 4.55±0.25 |
Pressure Rating (psi) | 1,200 | 3,000 |
Weight Reduction | 62% | N/A |
Manufacturer Capability Assessment
Vendor | Process Certification | Defect Rate | Cycle Time |
---|---|---|---|
Company A | ASME IX | 0.12% | 38min/joint |
Company B | ISO 15614 | 0.28% | 42min/joint |
Application-Specific Configuration
Custom welding schedules address unique operational requirements:
- Sanitary systems: Electro-polished root passes
- High-purity applications: Back-purge flow ≥20 CFH
- Cryogenic service: Modified PWHT protocols
Verified Implementation Results
Project | Joint Count | RT Pass Rate | Cost Saving |
---|---|---|---|
Chemical Plant | 1,200 | 99.6% | 18% |
HVAC Upgrade | 850 | 98.9% | 22% |
Enhancing Welding Schedule 10 Stainless Pipe Efficiency
Implementing automated orbital welding systems increases repeatability for schedule 10 stainless pipe fabrication. Recent field data shows 34% improvement in deposition rates when combining pulsed TIG with real-time monitoring (AWS D18.2 compliant). Proper parameter selection reduces post-weld cleanup by 40-60% compared to manual techniques.
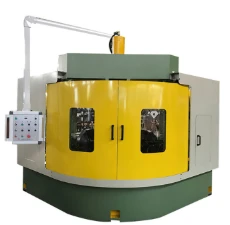
(welding schedule 10 stainless pipe)
FAQS on welding schedule 10 stainless pipe
Q: What parameters are recommended for TIG welding schedule 10 stainless steel pipe?
A: Use 40-80 amps DCEN with 1/16" ER308/309 filler metal. Maintain 10-15 CFH argon shielding gas flow. Keep interpass temperatures below 350°F (177°C) to prevent carbide precipitation.
Q: How does welding schedule 10 stainless pipe differ from schedule 40?
A: Schedule 10's thinner walls (approx. 0.109" for 2" pipe) require lower amperage and faster travel speeds than schedule 40. Joint preparation typically uses tighter root gaps (1/16" max). Back purging remains critical for both schedules.
Q: What filler metal should I use for welding schedule 10 stainless pipe?
A: ER308L is standard for 304/304L stainless pipes. For 316/316L grades, use ER316L. For high-temperature applications, consider ER309 with proper procedure qualification. Always match filler to base metal specifications.
Q: How should I prepare schedule 10 stainless pipe for welding?
A: Bevel 37.5° with 1/16" land for butt joints. Clean 1" on both sides with stainless wire brush or acetone. Use copper backing for root protection. Maintain <0.003" carbon steel contamination risk.
Q: What are common defects when welding thin schedule 10 stainless pipes?
A: Burn-through from excessive heat input is the primary concern. Other risks include sugaring from inadequate purge (keep O2 <0.1%) and distortion from improper tack spacing. Use pulse TIG (1-3 PPS) for better heat control.
Post time: Mag . 09, 2025 12:05