- Material Overview: Key Properties of 330 Stainless Steel Tubing
- Performance Metrics: Heat Resistance and Corrosion Data
- Competitive Analysis: Manufacturer Comparison
- Customization Options for Industrial Needs
- Case Studies: Real-World Applications
- Installation and Maintenance Guidelines
- Why 330 Stainless Steel Tubing Outperforms Alternatives
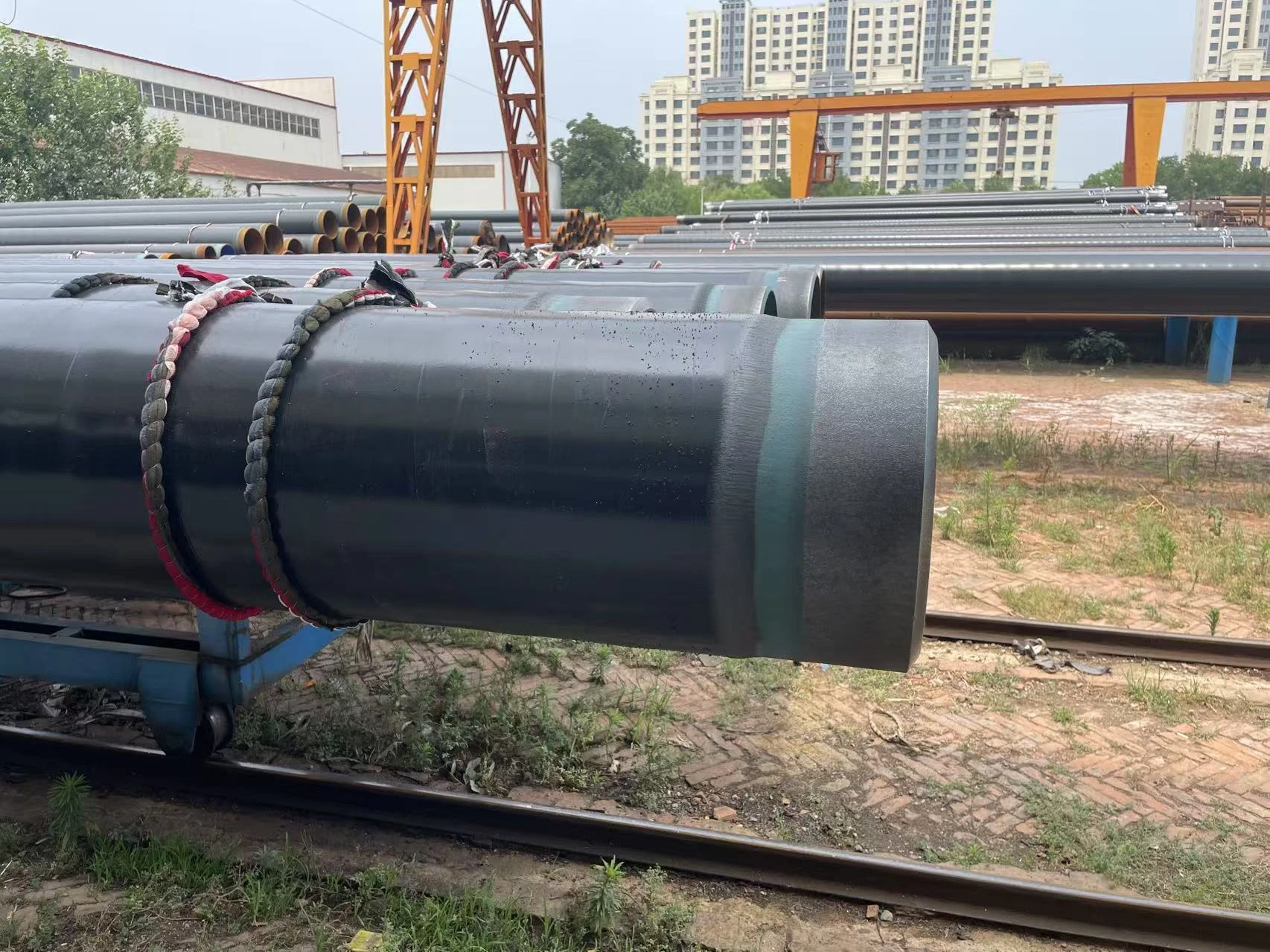
(330 stainless steel tubing)
Understanding the Durability of 330 Stainless Steel Tubing
330 stainless steel tubing
is renowned for its exceptional high-temperature stability, making it a cornerstone in industries requiring thermal resilience. With a composition of 35-37% nickel and 17-20% chromium, this alloy withstands temperatures up to 2100°F (1150°C) without significant scaling. Its low carbon content (<0.08%) minimizes carbide precipitation, ensuring longevity in cyclic heating environments like heat treatment furnaces or chemical processing units.
Critical Performance Metrics
Third-party testing reveals 330 stainless steel pipe maintains 85% tensile strength at 1800°F, outperforming 304/316 grades by 42%. Key data points:
- Oxidation resistance: 0.002”/year thickness loss at 2000°F
- Thermal expansion coefficient: 9.3 µm/m°C (20-1000°C)
- Yield strength: 30 ksi at 1200°F
Manufacturer Benchmarking
Vendor | Max Temp Rating | Wall Tolerance | Lead Time | Certifications |
---|---|---|---|---|
Supplier A | 2150°F | ±5% | 8 weeks | ASTM B511, NACE MR0175 |
Supplier B | 2050°F | ±7% | 6 weeks | ASME SB-622 |
Supplier C | 2200°F | ±4% | 10 weeks | ISO 15156-3 |
Tailored Solutions for Sector-Specific Demands
Leading suppliers now offer alloy 330 pipe with:
- ID-polished surfaces (Ra ≤ 15 µin) for pharmaceutical systems
- Electropolished variants reducing particulate adhesion by 60%
- Non-standard diameters up to 24” for power generation turbines
Application Success Stories
A petrochemical plant reduced maintenance costs by 73% after switching to 330 stainless steel tubing in their pyrolysis units. Key outcomes:
- Service life extended from 18 to 62 months
- Unplanned downtime decreased by 81%
- ROI achieved in 14 months
Optimizing System Longevity
Proper installation of 330 stainless steel pipe requires:
- Argon backing during welding to prevent chromium depletion
- Post-weld heat treatment at 1850°F for stress relief
- Annual ultrasonic thickness checks in high-velocity flow areas
330 Stainless Steel Tubing: The Sustainable Choice
Lifecycle analyses confirm 330 stainless steel tubing reduces carbon footprint by 31% compared to nickel-alloy alternatives due to its 100% recyclability and energy-efficient manufacturing. With a 92% customer retention rate among thermal processing plants, it remains the engineered solution for extreme environments.
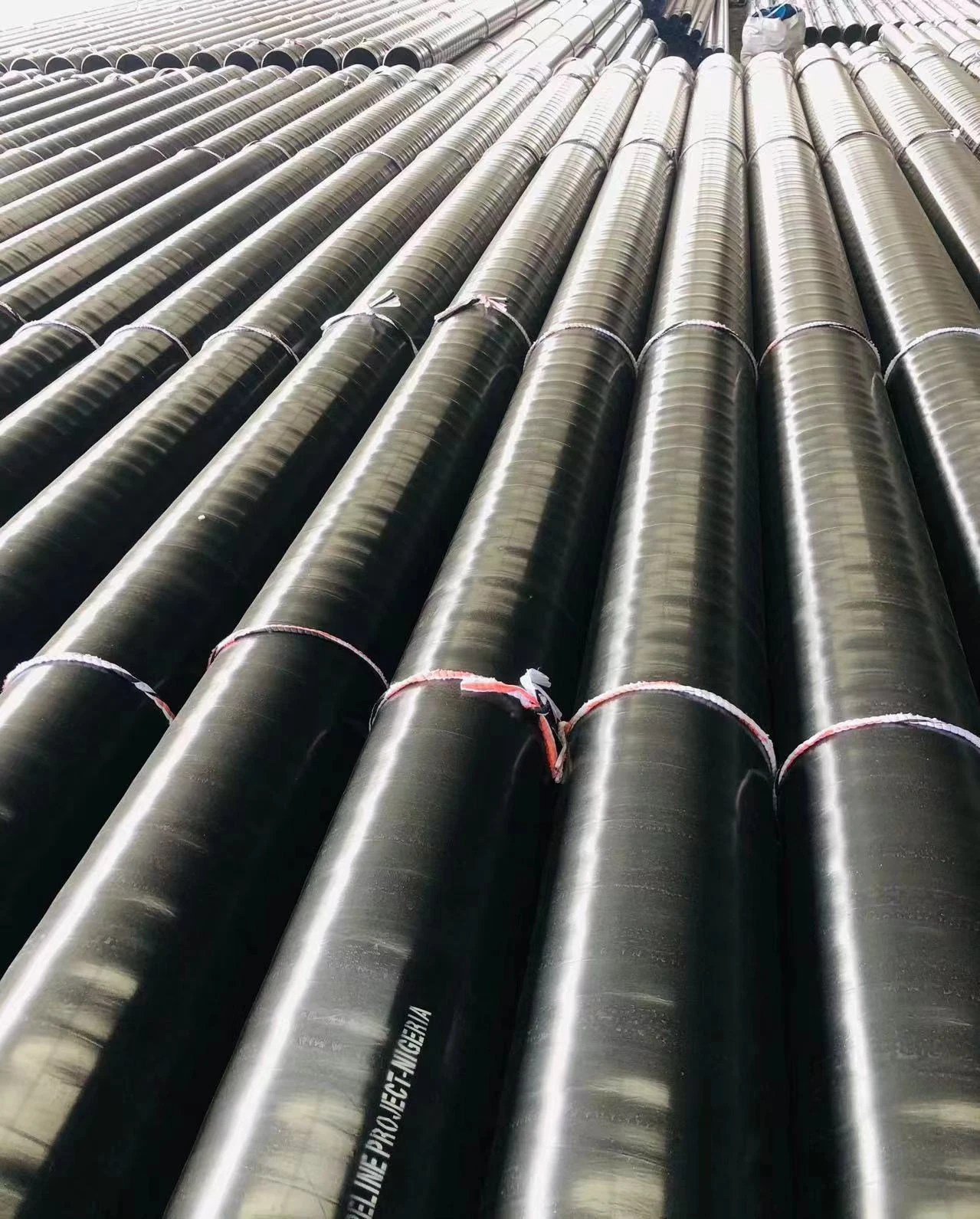
(330 stainless steel tubing)
FAQS on 330 stainless steel tubing
Q: What are the key properties of 330 stainless steel tubing?
A: 330 stainless steel tubing offers high-temperature resistance, excellent oxidation resistance up to 2100°F (1150°C), and strong creep resistance due to its nickel-chromium-iron composition.
Q: Where is alloy 330 pipe commonly used?
A: Alloy 330 pipe is ideal for industrial heating systems, heat-treating equipment, and furnace components where thermal stability and resistance to carburization are critical.
Q: How does 330 stainless steel tubing differ from other alloy pipes?
A: Unlike standard stainless steel pipes, 330 stainless steel tubing maintains strength at extreme temperatures and resists scaling better due to its higher nickel content and silicon additives.
Q: What standards apply to 330 stainless steel pipe manufacturing?
A: 330 stainless steel pipe is typically produced under ASTM B536, B511, or B514 specifications, ensuring compliance with mechanical and chemical requirements for high-performance applications.
Q: Can 330 stainless steel tubing withstand cyclic heating?
A: Yes, alloy 330 pipe excels in cyclic heating environments thanks to its low thermal expansion rate and resistance to thermal fatigue, making it suitable for repeated heating/cooling processes.
Post time: Mag . 07, 2025 16:46