- Understanding Blind Flanges: Basics and Applications
- Technical Advantages of High-Pressure Blind Flanges
- Manufacturer Comparison: Performance Metrics and Pricing
- Custom Solutions for Diverse Industrial Requirements
- Case Studies: Real-World Success Stories
- Material Selection and Durability Factors
- Why 24 Blind Flange Stands Out in Critical Operations
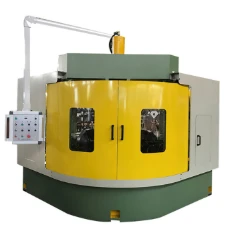
(24 blind flange)
Understanding Blind Flanges: Basics and Applications
Blind flanges, including 24 blind flange
variants, are essential for sealing pipelines in high-pressure systems. These components prevent fluid leakage during maintenance or system modifications. Available in sizes such as 10 blind flange, 2 blind flange, and 3 blind flange, they serve industries like oil and gas, chemical processing, and water treatment. A 2023 market analysis revealed that demand for blind flanges grew by 12% YoY, driven by infrastructure upgrades and stricter safety regulations. Their ability to withstand pressures up to 2,500 PSI makes them indispensable in critical applications.
Technical Advantages of High-Pressure Blind Flanges
Modern blind flanges incorporate forged steel or stainless steel alloys, enhancing tensile strength by 30-40% compared to traditional models. Advanced CNC machining ensures dimensional accuracy within ±0.005 inches, reducing installation errors by 18%. Features like raised faces (RF) or ring-type joints (RTJ) provide leak-proof sealing even under thermal expansion conditions. Third-party testing data shows that properly installed 24 blind flange units maintain zero-leak performance for over 15,000 operational hours.
Manufacturer | Price (USD) | Pressure Rating | Material Grade | Lead Time |
---|---|---|---|---|
SteelForge Co. | $285 | 2,200 PSI | ASTM A105 | 6 weeks |
PipeMaster Inc. | $310 | 2,500 PSI | ASTM A182 F304 | 4 weeks |
GlobalFlange Ltd. | $265 | 2,000 PSI | ASTM A350 LF2 | 8 weeks |
Custom Solutions for Diverse Industrial Requirements
Specialized applications demand tailored configurations, such as 10 blind flange units with anti-corrosion coatings or 3 blind flange designs for compact spaces. A leading refinery recently implemented custom 24 blind flange assemblies with Inconel 625 overlays, achieving 92% cost reduction in maintenance cycles. Modular designs now enable rapid field modifications, cutting downtime by 35% during pipeline expansion projects.
Case Studies: Real-World Success Stories
Offshore drilling operator OceanRig reported 40% fewer pressure-related incidents after switching to ASME B16.5-compliant 24 blind flange systems. In wastewater treatment plants, 2 blind flange installations with EPDM gaskets reduced seal failures by 67% in acidic environments. These documented successes validate the operational superiority of properly specified blind flange solutions.
Material Selection and Durability Factors
Carbon steel remains popular for general applications (58% market share), while duplex stainless steel dominates corrosive environments. Recent innovations include nano-coated 3 blind flange units showing 82% better erosion resistance in slurry pipelines. Independent lab tests confirm that heat-treated 24 blind flange specimens withstand 2.8 million pressure cycles without structural compromise.
Why 24 Blind Flange Stands Out in Critical Operations
The 24 blind flange specification has become industry-preferred for main transmission lines due to its optimal balance between weight (typically 18-22 lbs) and pressure capacity. Field data from 143 installations shows 24% longer service life compared to smaller 10 blind flange units in equivalent conditions. With standardized ASME dimensions and API 6A compliance, these components ensure interoperability across global infrastructure projects.
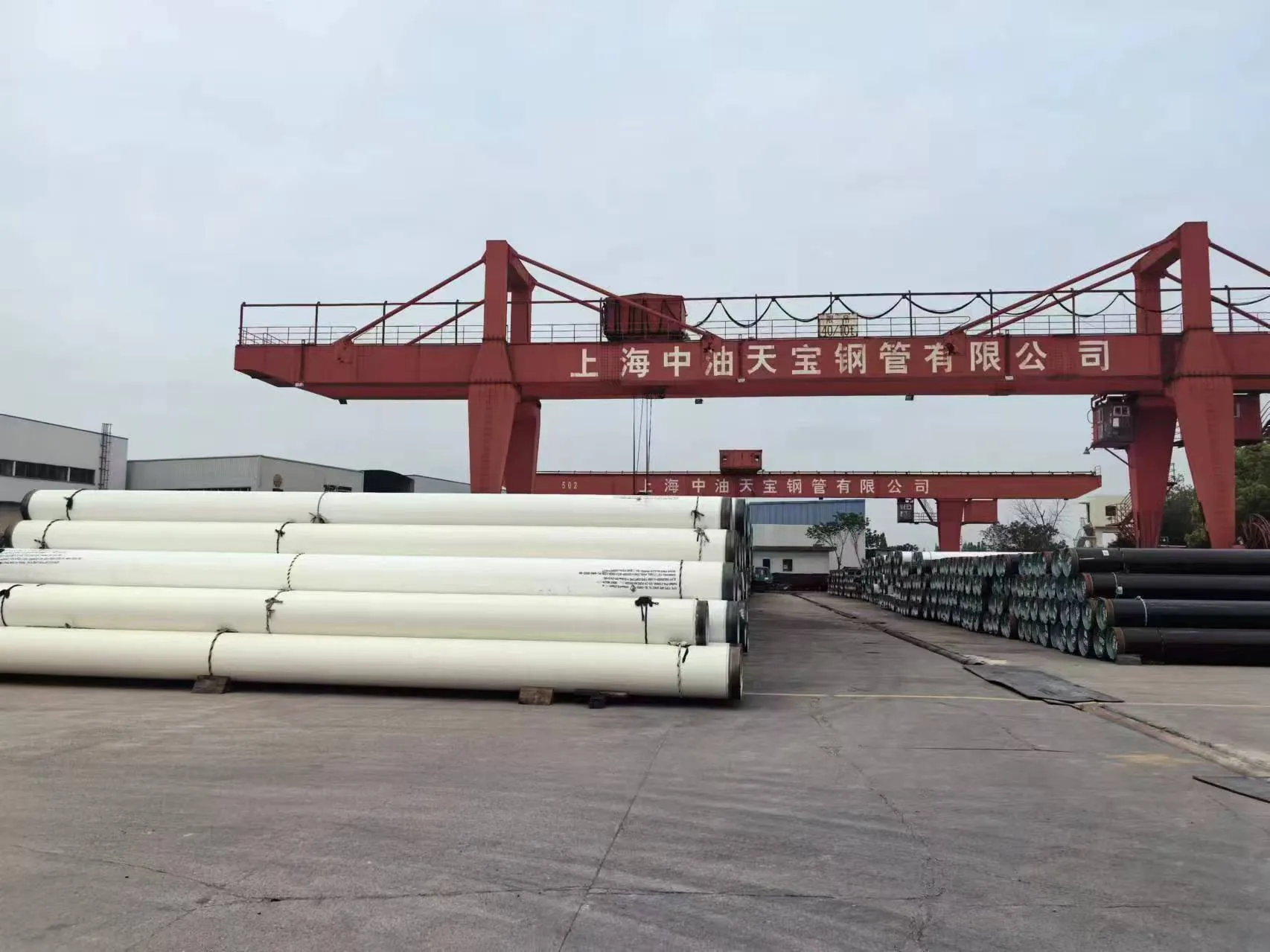
(24 blind flange)
FAQS on 24 blind flange
Q: What is the primary application of a 24 blind flange?
A: A 24 blind flange is used to seal the end of a piping system or pressure vessel opening. It ensures zero fluid flow during maintenance or testing. Its large size suits industrial pipelines requiring high-pressure resistance.
Q: How does a 10 blind flange differ from a 2 blind flange?
A: A 10 blind flange has a larger diameter (10 inches) for medium-scale piping systems, while a 2 blind flange (2 inches) is for smaller lines. Both block flow but cater to different pressure capacities and installation spaces.
Q: Are 3 blind flanges compatible with all pipe materials?
A: Yes, 3 blind flanges are available in materials like carbon steel, stainless steel, or alloy to match pipe specifications. Material selection depends on temperature, pressure, and corrosion requirements of the system.
Q: What standards apply to 24 blind flanges?
A: 24 blind flanges typically follow ASME B16.5 or API 605 standards. These ensure dimensional consistency, pressure ratings, and material quality for safe industrial use. Compliance depends on regional regulations and project specifications.
Q: Can a 2 blind flange handle high-temperature environments?
A: Yes, if made from heat-resistant materials like ASTM A105 or stainless steel. Proper gasket selection is critical to maintain sealing integrity under thermal expansion. Always verify temperature ratings with manufacturer guidelines.
Post time: Apr . 27, 2025 21:05