- Factors impacting 30x30 metal building expenses
- Steel construction's engineering benefits
- Leading manufacturer comparison (with price data)
- Design customization variables
- Performance metrics vs traditional builds
- Real-world implementation case studies
- Total investment considerations
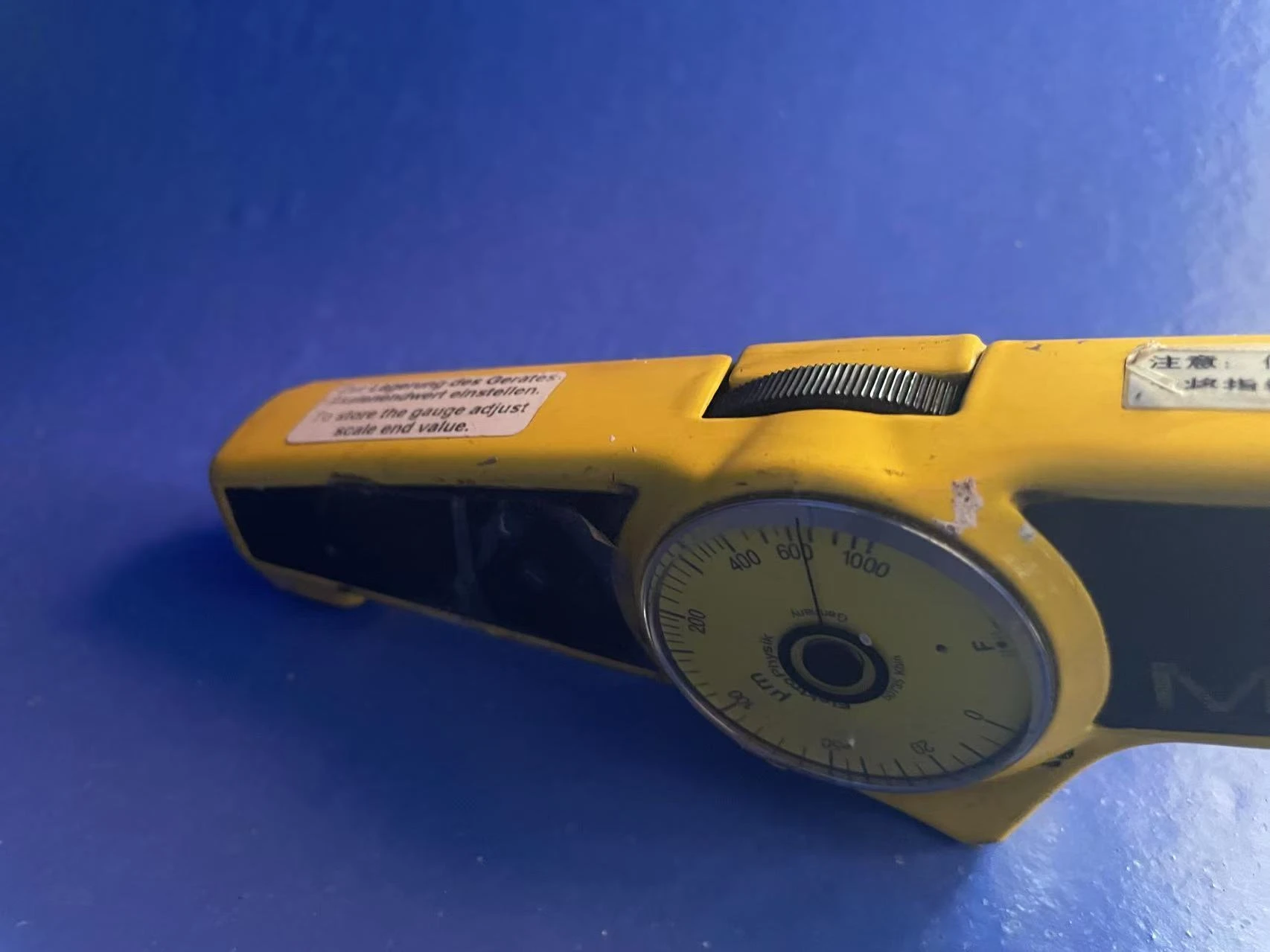
(cost of 30x30 metal building)
Breaking Down the Cost of 30x30 Metal Building Components
A standard 900 sq ft steel structure averages $14,500-$32,000 erected. This range fluctuates based on configuration complexity and material specifications. Essential expense drivers include:
Foundation & Substrate Preparation: $1,800-$4,200 for concrete slabs meeting PSI-3000 requirements. Frost line depth variations cause regional price differences of ±18%.
Structural Framework: Hot-dipped galvanized primary members (Grade-50 steel) represent 40-45% of material costs. Secondary purlins/girts add $1.25-$2.75 per linear foot.
Cladding Systems: 26-gauge Galvalume panels with Kynar coatings run $1.10-$2.80/sq ft installed. R-values influence insulation packages: Fiberglass batts (R-13) cost $0.85/sq ft versus spray foam's (R-28) $2.40/sq ft.
Engineering Advantages of Steel Frame Systems
Modern red-iron buildings deliver 50:1 span-to-depth ratios, enabling column-free interiors unachievable with wood frames. ASTM A572 steel components withstand 65psf snow loads and 130mph winds when properly engineered.
Accelerated construction timelines (typically 2-4 weeks) reduce labor expenditures by 35-45% versus stick-built alternatives. All-weather erection capabilities prevent seasonal delays that plague concrete projects during winter months.
Manufacturer Price Benchmark Analysis
Supplier | Base Package | Panel Warranty | Wind Rating | Price Range |
---|---|---|---|---|
ABC Steel Co | Primary frame + roofing | 40 years | 140 mph | $12,200-$16,800 |
XYZ Building Systems | Complete structural kit | 35 years | 150 mph | $15,600-$21,300 |
Metallic Structures Inc | Premium coating system | 45 years | 160 mph | $18,900-$25,700 |
Customization Cost Variables
Architectural enhancements alter baseline pricing:
Accessory Integration: 10x12 roll-up doors add $1,200-$1,800, while insulated personnel doors cost $480-$700. Continuous ridge vents provide ventilation at $15/linear foot.
Interior Configurations: Mezzanine installations consume 18-23% of budgets. Fire-rated drywall assemblies run $3.80/sq ft, significantly exceeding basic liner panel costs.
Exterior Treatments: Masonry veneer façades increase expenses by $10-$27/sq ft. Decorative eave trim packages typically add $780-$1,250 per building perimeter.
Performance Metrics Comparison
Steel buildings demonstrate measurable advantages:
Durability: Galvanized frames maintain structural integrity for 60+ years versus wood's 25-year lifecycle. Accelerated corrosion testing shows 0.5 mil/year degradation in industrial environments.
Operational Efficiency: Reflective roof coatings reduce cooling loads by 28% (ASHRAE 90.1 compliant). Annual maintenance costs average $0.18/sq ft compared to $0.43/sq ft for tilt-wall construction.
Implementation Case Studies
Equipment Storage (Kansas): 30x30 structure with 14' sidewalls and (2) 10x10 doors. Final cost: $19,800 including site preparation. Construction timeframe: 11 business days.
Artisan Workshop (Vermont): Fully insulated studio featuring 5" wall systems and skylights. Total investment: $31,200 with electrical systems. Permitting required 23 days despite winter conditions.
Factoring Total Cost of 30x30 Metal Building Ownership
Beyond initial construction, consider capitalization expenses over 30 years. Steel buildings achieve 95% scrap value recovery versus traditional construction. Commercial financing options include:
• 60-month equipment loans: 5.75-7.25% APR
• Real estate term loans: 15-25 year amortization
• Municipal incentives: 12-18% tax abatements available in 29 states
Structural warranties typically cover 30-50 years depending on coating systems selected. Post-frame steel consistently delivers 35-50% lifecycle savings versus conventional materials across a 30x30 footprint.
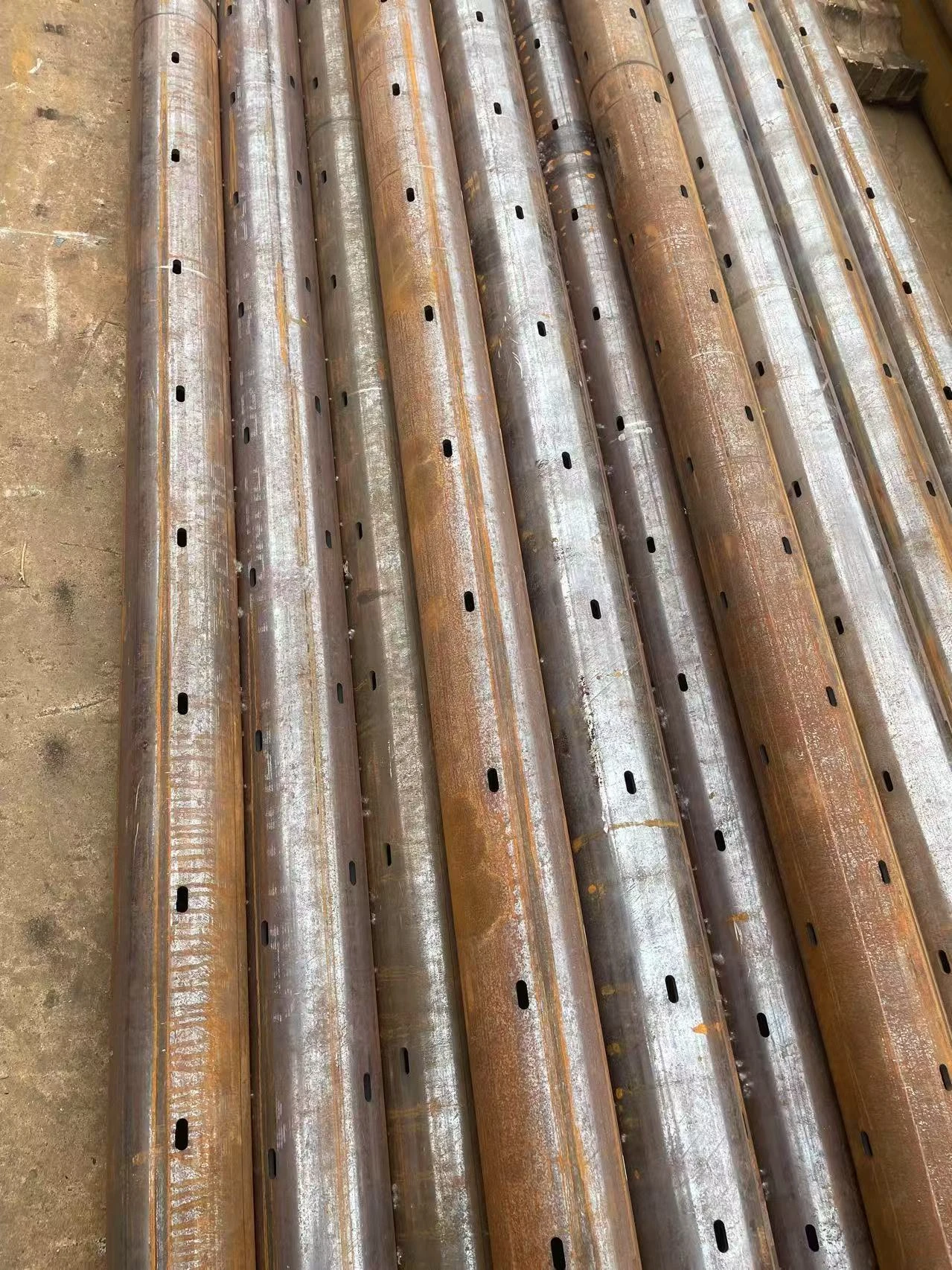
(cost of 30x30 metal building)
FAQS on cost of 30x30 metal building
Q: What is the average cost of a 30x30 metal building?
A: The average cost of a 30x30 metal building ranges from $15,000 to $35,000, depending on materials, design, and location. Basic kits start around $10,000, while customized structures with insulation and finishes can exceed $40,000.
Q: What factors influence the 30x30 metal building cost?
A: Key factors include steel prices, foundation type, labor costs, insulation, doors/windows, and local building codes. Roof style (e.g., vertical vs. horizontal) and interior finishes also impact the final price.
Q: How much does a 30x30 metal building cost per square foot?
A: A 30x30 metal building typically costs $15-$35 per square foot for basic structures. Premium designs with added features may reach $50+ per square foot, excluding site preparation and permits.
Q: Does the cost of a 30x30 metal building include installation?
A: Most kit prices exclude installation, which adds $5-$15 per square foot. Full-service contractors may charge $25,000-$50,000 total, including materials, labor, and foundation work.
Q: Are there hidden costs in 30x30 metal building projects?
A: Common hidden costs include land grading ($1,000-$5,000), permits ($500-$2,000), utility connections, and interior finishing. Always budget 10-15% extra for unexpected expenses.
Post time: Juin . 02, 2025 20:08