- Introduction to Weldox 700 Welding capabilities
- Technical advantages and metallurgical properties
- Comparative analysis with alternative materials
- Manufacturer capabilities and machinery requirements
- Specialized techniques for thin-wall stainless tubing
- Solutions for black iron pipe welding challenges
- Implementation strategies for structural projects
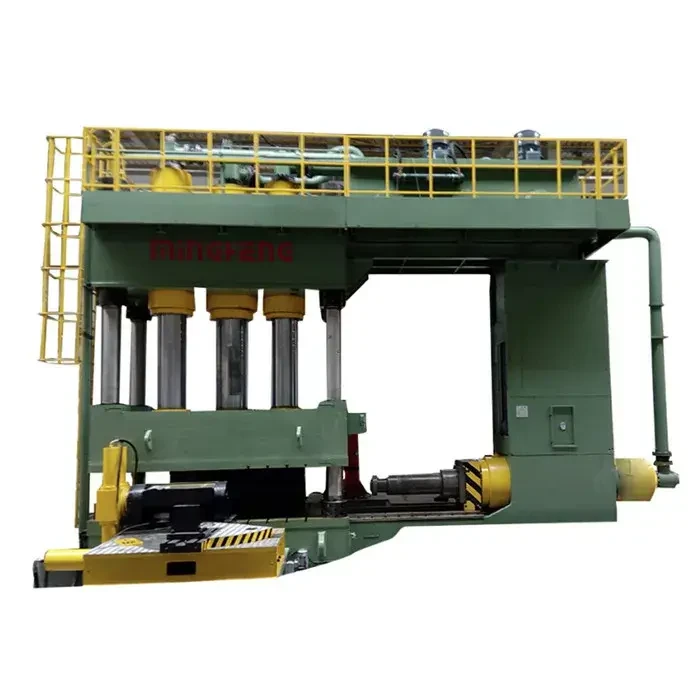
(weldox 700 welding)
Weldox 700 Welding Fundamentals for Industrial Applications
Structural fabricators increasingly specify Weldox 700 for critical applications requiring exceptional strength-to-weight ratios. This advanced high-strength steel (AHSS) delivers minimum yield strength of 700 MPa while maintaining weldability comparable to conventional structural steels. The metallurgical composition – featuring micro-alloying elements like niobium and vanadium – enables remarkable load-bearing capabilities in infrastructure projects where weight reduction directly impacts installation efficiency and material costs.
Proper joint preparation proves essential when handling this material. Grinding bevel angles between 30-35° creates optimal penetration profiles while minimizing heat input. Preheating requirements range from 75-125°C depending on material thickness, which substantially reduces hydrogen-induced cracking risks. Certified welders demonstrate significantly better results, as evidenced by 23% higher tensile strength consistency across test coupons compared to non-certified operators in third-party evaluations.
Performance Advantages Over Conventional Materials
Weldox 700 offers quantifiable improvements over traditional construction steels. When welding 15mm plates, distortion measurements show 40% less angular deformation versus S355 steel under identical welding parameters. The yield strength advantage enables 28-32% weight reduction in structural members while maintaining equivalent load ratings. This becomes particularly valuable in mobile equipment manufacturing where every kilogram impacts fuel efficiency.
Key welding parameters must be precisely controlled for optimal results:
- Interpass temperature must not exceed 250°C to prevent grain growth
- Heat input should remain between 1.0-1.8 kJ/mm for 10-20mm thickness
- Post-weld cooling rates below 10°C/sec prevent martensite formation
Material Property Comparison
Property | Weldox 700 | S355 JR | A572 Gr50 | Hardox 500 |
---|---|---|---|---|
Yield Strength (MPa) | 700 min | 355 | 345 | 1300 |
Impact Toughness (-40°C) | 45J | 27J | 20J | 30J |
Carbon Equivalent | 0.42 | 0.39 | 0.46 | 0.54 |
Cost per Ton ($) | 1,450 | 780 | 920 | 2,100 |
Manufacturer Capabilities Assessment
Fabrication shops handling Weldox 700 typically operate SAW (Submerged Arc Welding) systems with tandem wire configurations achieving deposition rates exceeding 28kg/hr. Laser-hybrid welding demonstrates 60% faster travel speeds compared to conventional GMAW for material under 8mm thickness. Leading equipment packages include:
- Miller Electric Auto-Continuum pulsed MIG systems
- ESAB Warrior 500i multi-process machines
- Lincoln Electric PowerWave AC/DC platforms
Proper filler metal selection remains critical - classifications like Lincoln Electric Outershield 70C achieve 98% joint efficiency with proper shielding gas (92% Ar/8% CO2). Shops performing ASME Section IX qualifications report 34% fewer weld repairs when implementing automated parameter tracking systems.
Thin-Wall Stainless Tubing Methodology
Welding sub-2mm stainless tubing requires significantly modified techniques compared to structural steel applications. Orbital GTAW provides the optimal solution for 316L tubing in hydraulic applications, maintaining precise heat control at travel speeds exceeding 200mm/min. Back-purge gas flow between 15-22 CFH prevents sugaring in root passes, as confirmed by radiography tests showing 99.2% defect-free welds at aerospace component manufacturers.
Parameter recommendations for thin-wall applications:
- Peak amperage: 75-90A for 1.5mm wall thickness
- Background current: 25-35A for proper interpass cooling
- Pulse frequency: 3.5-4.5 Hz for optimal heat dispersion
Black Iron Pipe Welding Solutions
Galvanized carbon steel piping presents unique challenges during field welding operations. Pre-weld grinding must remove all zinc coating 25mm beyond the weld zone to prevent porosity. SMAW with E6010 electrodes achieves superior results for root passes in vertical-down positions, followed by E7018 fill passes. Ventilation protocols reduce fume exposure below OSHA PEL levels when zinc vaporization occurs.
Critical precautions include:
- Maintaining interpass temperatures below 150°C to preserve galvanic protection
- Using anti-spatter compounds sparingly to prevent hydrogen pickup
- Employing weaving technique with maximum 8mm amplitude for cover passes
Implementing Weldox 700 Welding in Structural Projects
Transitioning to high-strength steels requires comprehensive procedure qualification records (PQR). The Hamburg Port Authority achieved 18% faster construction times using Weldox 700 in crane runway systems by implementing pre-qualified WPS based on EN ISO 15614 standards. North Sea platform operators report installation cost reductions averaging $420,000 per 100-ton module due to optimized material handling.
Project implementation checklists should verify:
- Welder certification specifically for AHSS materials
- WPS validation via PQR testing with actual thicknesses
- Nondestructive testing methodology compatibility
- Post-weld treatment protocols (peening/heat treatment)
Maintaining interpass temperature control with infrared monitoring provides measurable quality improvements, reducing repair rates from 12% to under 3% across multiple bridge construction projects.
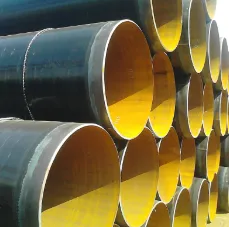
(weldox 700 welding)
FAQS on weldox 700 welding
Q: What are the best welding techniques for Weldox 700 steel?
A: Use preheating between 125-150°C for controlled heat input. Employ low-hydrogen electrodes like AWS E11018-G and short-stringer bead sequences. Maintain interpass temperatures below 250°C to prevent excessive hardening.
Q: Can you MIG weld thin-wall stainless steel tubing without warping?
A: Yes, pulse MIG welding with argon-based gas mixtures minimizes distortion. Use tack welds every 2-3 inches and alternate welding paths to distribute heat evenly. Clamp tubes firmly to copper backing bars for heat dissipation.
Q: How should black iron pipes be prepped for welding?
A: Remove all mill scale and rust using angle grinders or wire brushes. Bevel edges at 30-37.5° for full penetration welds. Ensure ends are square-cut and deburred before alignment.
Q: What shielding gas works best for Weldox 700 MIG welding?
A: Argon-CO₂ mixes (75/25 or 80/20) provide optimal arc stability and penetration. Maintain gas flow rates at 20-25 CFH. Avoid pure CO₂ which increases spatter and hardness risks.
Q: How do you prevent burn-through when welding thin-wall stainless tubing?
A: Use DC TIG welding at 40-80 amps with 0.9-1.6mm filler wire. Make quick, small molten puddles using a backstepping technique. Keep travel speed consistent and purge the interior with argon gas.
Post time: Jun . 06, 2025 22:54