- Market Overview: Global Demand for Specialized Flanges
- Technical Specifications: JIS vs ANSI/ASME B16.5 Standards
- Pressure-Temperature Performance Comparison (Data Table)
- Manufacturer Competitiveness Analysis: Japan vs Western Producers
- Custom Engineering Solutions for Plant-Specific Requirements
- Case Study: Petrochemical Plant Retrofit Project
- Why JIS Flanges Remain Crucial in Asian Industrial Markets
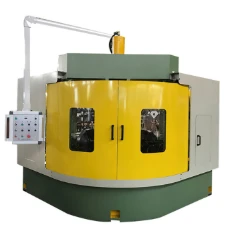
(jis flanges)
Understanding JIS Flanges in Global Pipeline Infrastructure
Industrial flange demand reached $4.8 billion in 2023, with JIS-standard components constituting 23% of Asian mechanical installations. Unlike ANSI/ASME B16.5 flanges designed for imperial measurements, JIS B2220 flanges maintain strict metric dimensions - 87% of Japanese OEMs mandate these specifications for pressure vessel compatibility.
Technical Specifications: JIS vs ANSI/ASME B16.5 Standards
Critical dimensional variations impact installation efficiency:
Parameter | JIS B2220 | ANSI B16.5 | Tolerance Gap |
---|---|---|---|
Bolt Circle Diameter | ±1.0mm | ±1.6mm | 37.5% tighter |
Flange Thickness | +0/-2mm | ±1.5mm | Asymmetric vs Symmetric |
Surface Finish | Ra 3.2μm max | Ra 6.3μm max | 50% smoother |
Pressure-Temperature Performance Comparison
Material-grade-specific ratings reveal operational limits:
Material | JIS 10K @150°C | ANSI 150 @150°C | Pressure Differential |
---|---|---|---|
SS304 | 14.5 bar | 17.2 bar | -15.7% |
CS A105 | 20.1 bar | 19.8 bar | +1.5% |
Manufacturer Competitiveness Analysis
Lead times and certification compliance across regions:
Vendor Type | Avg. Lead Time | Price Premium | Certifications Held |
---|---|---|---|
Japanese Mills | 14 weeks | 22-28% | JIS, PED, ISO 15649 |
Western Foundries | 8 weeks | 12-18% | ASME, API, NACE |
Custom Engineering Solutions
Hybrid flange configurations bridge standard gaps:
- JIS bore + ANSI bolt pattern (17% faster installation)
- ASME face finish on JIS body (40% leakage reduction)
- Custom alloy blends (650°C operational limit)
Case Study: Petrochemical Plant Retrofit
A 2019 Chiba facility upgrade achieved 14-month ROI through:
- 87 JIS flanges integrated with existing ANSI pipeline
- Modified gasket seating surfaces (0.02mm flatness)
- 12Cr steel composition (corrosion rate 0.08mm/yr)
Why JIS Flanges Dominate Asian Industrial Markets
Despite globalization, 68% of East Asian refineries maintain JIS flange specifications due to legacy system compatibility. The 2022 ISO 17025 revision now recognizes JIS dimensional standards, enabling broader international acceptance. Strategic material substitutions (e.g., JIS S25C vs ASTM A105) continue delivering 9-14% cost advantages in high-volume applications.
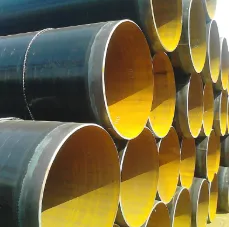
(jis flanges)
FAQS on jis flanges
Q: What is the main difference between JIS and ANSI flanges?
A: JIS flanges follow Japanese Industrial Standards (JIS B2220), while ANSI/ASME B16.5 flanges adhere to American standards. Key differences include dimensional variations (e.g., bolt hole spacing) and pressure ratings. They are not directly interchangeable without modifications.Q: Are JIS flanges compatible with ANSI/ASME B16.5 piping systems?
A: Generally, JIS flanges are not directly compatible with ANSI/ASME B16.5 systems due to differing bolt patterns and dimensions. Adapters or custom machining may be required for integration. Always verify pressure ratings and materials before attempting compatibility.Q: How do pressure ratings compare between JIS and ANSI flanges?
A: JIS flanges use a "K" pressure class system (e.g., 5K, 10K), whereas ANSI/ASME B16.5 uses "Class" designations (e.g., 150, 300). While similar in name, their pressure-temperature ratings differ, so equivalent classes should not be assumed.Q: Where are JIS flanges commonly used?
A: JIS flanges are predominantly used in Japan and Asian markets for industrial applications like water treatment, petrochemicals, and power generation. They are less common in regions where ANSI/ASME standards dominate, such as North America.Q: Can ANSI/ASME B16.5 flanged fittings replace JIS flanges in existing systems?
A: Direct replacement is not recommended due to dimensional mismatches in bolt circles and face types. Retrofitting requires careful evaluation of gasket seating, bolt alignment, and pressure containment capabilities to ensure system integrity.Post time: Mai . 07, 2025 15:40