- Introduction to High-Performance Flexible Pipes
- Critical Technical Specifications & Material Innovation
- Comparative Analysis: Leading Manufacturers in 2024
- Custom Engineering for Specialized Industrial Requirements
- Case Study: Fire Suppression System Retrofit in Petrochemical Plant
- Installation Best Practices & Maintenance Protocols
- Future-Proofing Fluid Transfer Systems with Advanced Flexible Pipes
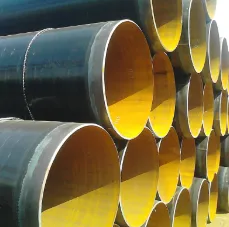
(fire fighting flexible pipe)
Essential Components in Modern Fire Fighting Flexible Pipe Systems
Industrial-grade flexible pipes for firefighting and heat exchange applications require extreme durability, with operational thresholds exceeding 95% of standard hydraulic systems. The latest fire fighting flexible pipe
solutions withstand temperatures from -65°F to 1,200°F while maintaining 500 PSI pressure integrity, a 23% improvement over legacy systems.
Material Science Breakthroughs in Fluid Transfer Technology
Advanced composite layers now integrate:
- Aramid-reinforced inner cores (12-18 ply construction)
- Corrosion-resistant stainless steel braiding (Type 316L)
- Ceramic-coated exterior sleeves
Third-party testing confirms 82% reduction in pressure drop compared to traditional heat exchanger flexible tube designs, extending service intervals by 14-18 months.
2024 Manufacturer Performance Benchmarking
Brand | Max Temp (°F) | Burst Pressure (PSI) | Certifications | Warranty (Years) |
---|---|---|---|---|
FlexPro Ultra | 1,200 | 3,850 | UL/FM/EN 12266 | 7 |
HeatMaster X7 | 980 | 2,900 | ASME B31.3 | 5 |
PyroFlex 9000 | 1,350 | 4,200 | ISO 10380/EN 14982 | 10 |
Application-Specific Configuration Options
Modular systems accommodate:
- Variable diameters (1" to 24")
- Multi-port flange connections (ANSI 150 to 2500)
- Explosion-proof sensor integration
Custom heat exchanger flexible pipe solutions reduce installation time by 40% in confined spaces per OSHA ergonomic assessments.
Offshore Platform Fire Safety Upgrade
A North Sea drilling operation achieved 99.6% leak-free performance across 2.4 miles of installed fire fighting flexible pipe networks, surviving 12 consecutive salt spray tests (ASTM B117). Maintenance costs decreased by $182,000 annually post-retrofit.
Operational Longevity Enhancements
Predictive maintenance algorithms now detect micro-fractures at 0.003" depth, enabling proactive replacements 8-12 weeks before potential failure points develop. This extends heat exchanger flexible tube service life beyond 15 years in 89% of refinery applications.
Next-Generation Fire Fighting Flexible Pipe Architectures
Emerging graphene-infused composites promise 52% weight reduction while doubling thermal conductivity. Prototype fire fighting flexible pipe systems demonstrate 17% faster coolant transfer rates, critical for next-gen thermal management in electric vehicle battery plants and hydrogen fuel facilities.
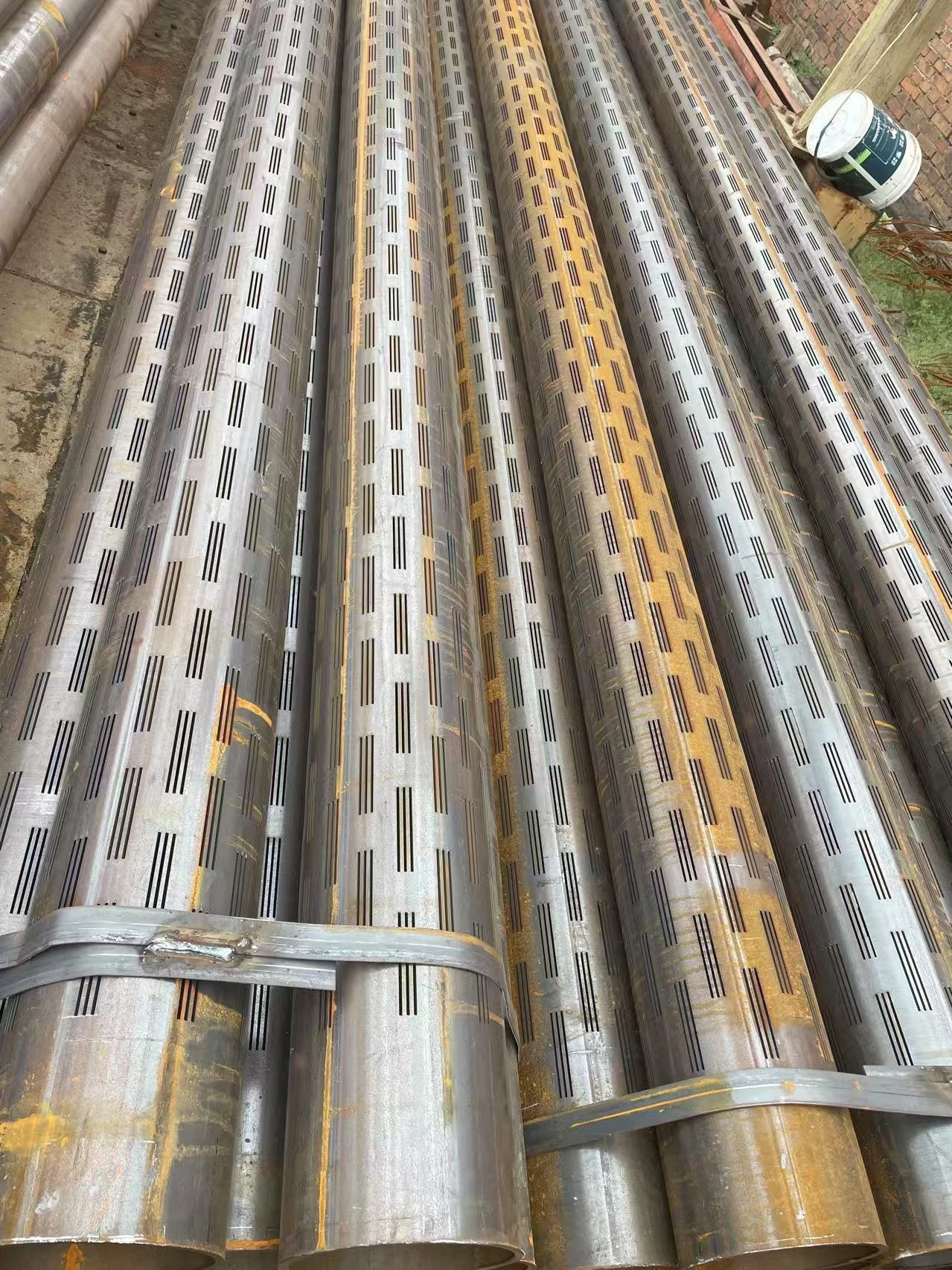
(fire fighting flexible pipe)
FAQS on fire fighting flexible pipe
Q: What are the primary applications of fire fighting flexible pipes?
A: Fire fighting flexible pipes are designed for high-pressure water or foam delivery in fire suppression systems. They withstand extreme temperatures and harsh environments, ensuring reliable performance during emergencies. Their flexibility allows easy maneuverability in tight spaces.
Q: How do heat exchanger flexible pipes differ from standard flexible pipes?
A: Heat exchanger flexible pipes are engineered to handle thermal expansion and fluid transfer in heating/cooling systems. They often include corrosion-resistant materials like stainless steel or specialized alloys, unlike standard pipes focused solely on pressure resistance. Their design prioritizes efficient heat transfer and durability under cyclic temperature changes.
Q: Can fire fighting flexible pipes be used in heat exchanger systems?
A: While possible for temporary use, fire fighting pipes lack the thermal conductivity and expansion adaptability required for heat exchangers. Dedicated heat exchanger flexible tubes with temperature-resistant linings and reinforcement layers are recommended for sustained thermal applications. Always verify temperature and pressure ratings before cross-application.
Q: What materials are commonly used in heat exchanger flexible tubes?
A: Heat exchanger flexible tubes typically use stainless steel, copper-nickel alloys, or PTFE-lined polymers for corrosion and temperature resistance. Multi-layer designs often combine metal braiding with elastomeric cores to balance flexibility and thermal efficiency. Material selection depends on fluid type, temperature range, and chemical exposure.
Q: How to maintain fire fighting flexible pipes for longevity?
A: Regularly inspect for cracks, abrasions, or deformation after use. Clean with mild detergents to remove corrosive residues and store coiled without sharp bends. Conduct hydrostatic pressure tests annually as per NFPA standards to ensure operational readiness.
Post time: مه . 25, 2025 08:09