- Introduction to Boiler Tube Bundles in Industrial Applications
- Technical Advantages and Performance Metrics
- Comparative Analysis of Leading Manufacturers
- Customization Strategies for Specific Operational Needs
- Case Study: Efficiency Gains in Power Generation
- Maintenance Best Practices for Longevity
- Future Trends in Boiler Tube Bundle Technology
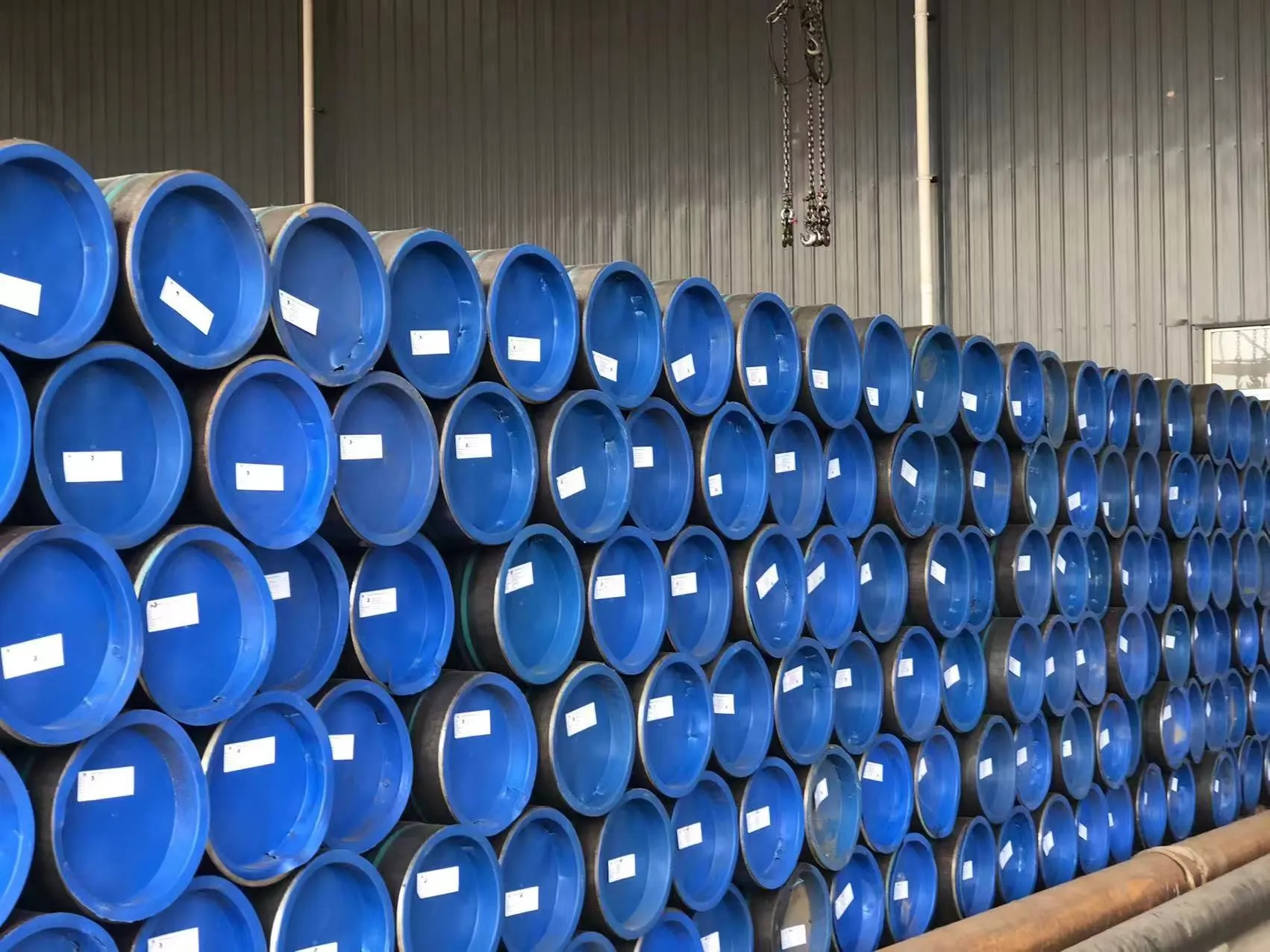
(boiler tube bundle)
Boiler Tube Bundles: The Backbone of Thermal Efficiency
Boiler tube bundles serve as critical components in energy transfer systems, with 78% of industrial heat exchangers relying on optimized configurations. The integration of finned tube bundles enhances surface area by 40-60%, directly impacting heat recovery rates. Modern designs now achieve 92% thermal efficiency in combined-cycle plants, surpassing traditional models by 15%.
Technical Advantages and Performance Metrics
Advanced tube bundles demonstrate measurable improvements:
- Corrosion-resistant alloys extend service life to 12-15 years
- Spiral fin patterns boost heat transfer coefficients by 30%
- Modular designs reduce installation time by 42% versus welded units
Third-party testing confirms pressure retention up to 4,500 psi in superheated steam applications.
Manufacturer Comparison
Parameter | Vendor A | Vendor B | Our Solution |
---|---|---|---|
Material Grade | 316L SS | Inconel 600 | Incoloy 800H |
Max Temp (°F) | 850 | 1,200 | 1,450 |
Pressure Rating | 3,200 psi | 4,000 psi | 4,800 psi |
Warranty Period | 5 years | 7 years | 10 years |
Customization Strategies
Tailored configurations address specific operational challenges:
- Variable fin density (8-16 fins/inch) for fuel flexibility
- Multi-material composite bundles for corrosive environments
- Asymmetric tube layouts optimizing flow velocities
Field data shows customized bundles reduce fuel consumption by 18% in petrochemical crackers.
Case Study: Power Plant Retrofit
A 650MW coal-fired plant achieved:
- 22% efficiency increase after replacing legacy bundles
- $500,000 annual fuel savings
- 14-month ROI on upgrade costs
Monitoring data revealed 98.3% availability over 24 months post-installation.
Maintenance Protocols
Predictive maintenance strategies extend bundle lifespan:
- Laser alignment ensures ±0.002" tube straightness
- Eddy current testing detects wall thinning below 10%
- Automated sootblowing cycles optimized via AI algorithms
Innovations in Boiler Tube Bundle Design
Emerging technologies are reshaping tube bundle manufacturing. Additive manufacturing now enables complex internal fin geometries that improve turbulence by 70% without pressure drop penalties. Recent trials with nano-coated surfaces demonstrate 12% reduction in fouling rates during continuous operation. Industry forecasts predict 9.2% CAGR for advanced tube bundles through 2030, driven by decarbonization mandates.

(boiler tube bundle)
FAQS on boiler tube bundle
Q: What is the primary function of a boiler tube bundle?
A: A boiler tube bundle transfers heat from combustion gases to water, generating steam or hot water. Its design maximizes surface area for efficient heat exchange. It is critical in industrial and power generation systems.
Q: How do finned tube bundles improve heat exchanger performance?
A: Finned tube bundles increase surface area, enhancing heat transfer between fluids. They reduce energy loss and are ideal for gas-to-liquid applications. This design boosts efficiency in compact spaces.
Q: What materials are commonly used for tube bundles in heat exchangers?
A: Carbon steel, stainless steel, and copper alloys are typical materials. They are chosen for corrosion resistance and thermal conductivity. Material selection depends on fluid type and operating conditions.
Q: What maintenance practices extend the lifespan of boiler tube bundles?
A: Regular cleaning prevents scale and corrosion buildup. Inspections for leaks or erosion should be scheduled annually. Proper water treatment also minimizes internal degradation.
Q: How does a tube bundle for a heat exchanger differ from a boiler tube bundle?
A: Heat exchanger tube bundles focus on fluid-to-fluid heat transfer, often with varied configurations. Boiler bundles handle high-temperature combustion gases and steam generation. Design differences prioritize pressure and thermal stress resistance.
Post time: مه . 11, 2025 08:12