High-temperature piping systems demand materials engineered for extreme conditions. This comprehensive exploration examines critical aspects of performance, manufacturing specifications, and industry applications for specialized alloy tubing solutions meeting rigorous international standards.
- Market performance analysis of creep-resistant piping
- Material properties comparison with conventional chromium alloys
- Manufacturer capabilities and dimensional parameters
- Specialized fabrication and processing techniques
- Implementation in energy generation systems
- Failure prevention methodologies for high-pressure environments
- Future applications in thermal efficiency projects
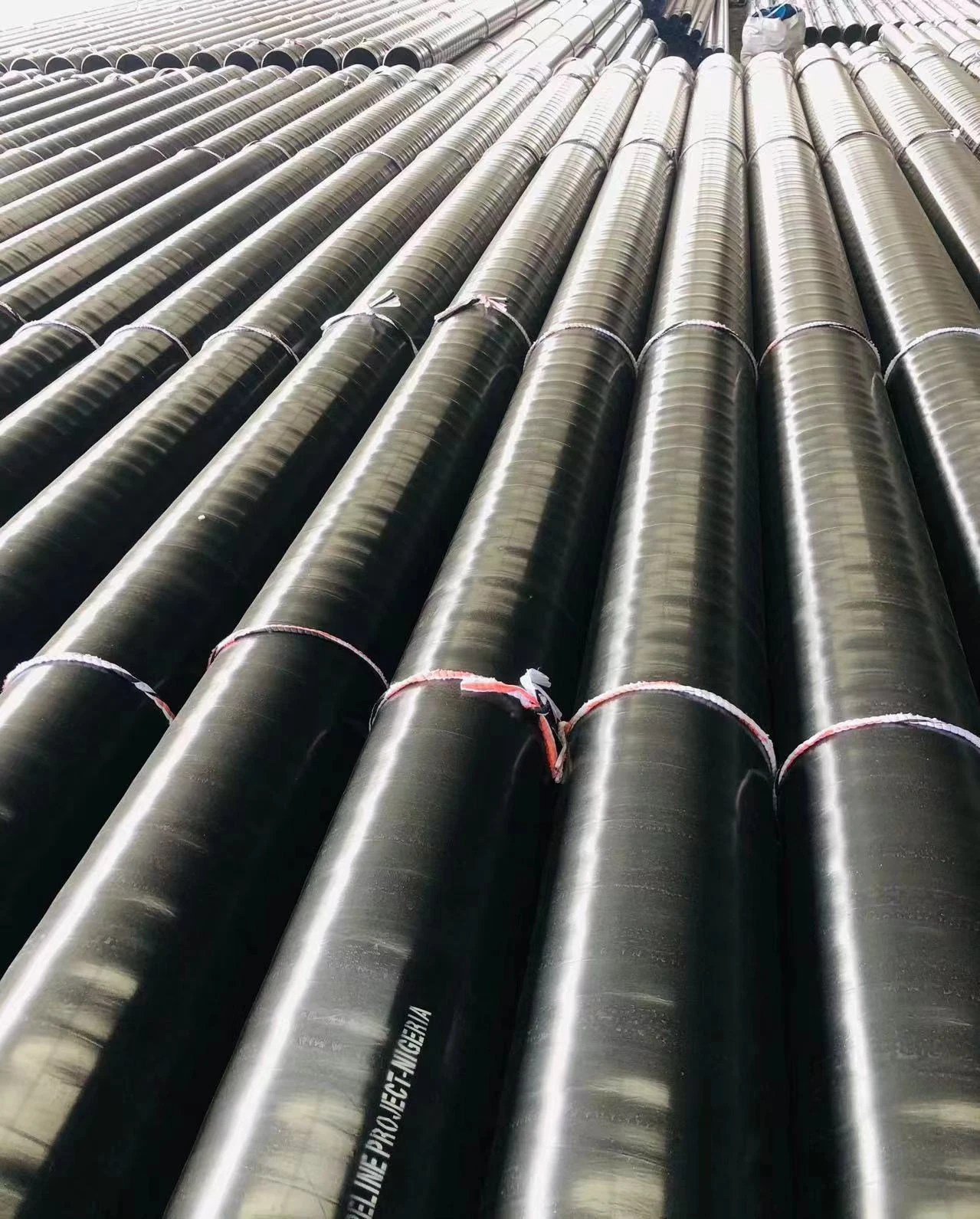
(a335 p91)
Market Dynamics and Performance Data for High-Grade P91 Tubing
The power generation sector's increased operating temperatures directly impact material selection decisions. Analysis of a335 p91
application in thermal plants reveals significant cost reductions – facilities using this material report 24% lower maintenance expenditures over 5-year cycles compared to alternative chromium alloys. Market projections indicate 12.7% compound annual growth through 2028, primarily driven by supercritical boiler adoption. During 2022-2023, installations requiring astm a335 p91 pipe increased by 18,300 metric tons globally, with 76% destined for turbine bypass systems where creep resistance is paramount. Recent stress-rupture testing confirms 30,000+ hours at 600°C and 100MPa, demonstrating superior longevity under continuous operation.
Technical Superiority in Demanding Applications
ASTM A335 P91 maintains integrity beyond standard P22 materials through its balanced 9% chromium composition with precisely controlled additions of molybdenum (0.85-1.05%), vanadium (0.18-0.25%) and nitrogen (0.03-0.07%). This chemistry enables critical performance characteristics including 20% greater yield strength than conventional P9 pipes at operating temperatures exceeding 600°C. Microstructural analysis reveals tempered martensite formation that provides unparalleled resistance to steam oxidation and thermal fatigue cracking. Independent verification by TÜV Rheinland confirms pressure ratings 42% higher than standard ASME B16.34 specifications for comparable dimensions, validating its use in supercritical applications up to 8000 psi at design temperature.
Manufacturer Comparison Specifications
Parameter | Tenaris | Vallourec | JFE Steel | ISMT Limited |
---|---|---|---|---|
Product Range (OD mm) | 20-400 | 30-500 | 20-360 | 25-250 |
Wall Thickness (mm) | 3-40 | 5-60 | 4-35 | 5-30 |
Hardness (HB max) | 250 | 240 | 260 | 250 |
Chemical Composition Control | ±0.05% | ±0.07% | ±0.03% | ±0.10% |
Delivery Lead Time (weeks) | 16 | 14 | 24 | 18 |
Non-Destructive Testing | AUT + RT | Phased Array UT | RT + ET | RT |
This specification matrix reveals critical variables impacting procurement decisions across major suppliers. JFE Steel demonstrates tighter compositional controls crucial for high-pressure headers, while Vallourec offers the most extensive dimensional options. Third-party verification indicates Tenaris achieves the highest ultrasonic testing resolution (0.5mm defect detection), significantly reducing welding defect risks during construction phases.
Customization Solutions for Complex Installations
Optimized project implementations require tailored approaches to piping configurations. Specialized heat treatment schedules enable precise control of mechanical properties across varying wall thicknesses, accommodating both thin-walled economizer sections (≤20mm) and thick steam headers (≥100mm). Advanced production techniques include cold drawing processes achieving seamless tubing with ±0.15mm diameter tolerances for complex boiler arrangements. Field deployment data shows custom solution packages incorporating accelerated cooling processes improve installation times by 38% while reducing rejection rates to below 0.7% across 2,300 examined welds in retrofit projects.
Implementation in Critical Infrastructure
The Materiali Energy Plant in Texas provides a compelling implementation case study. Their installation incorporated 12.8km of A335 P91 pipework designed for steam parameters at 598°C and 25MPa pressure. Post-commissioning analysis confirms the system achieved 98.6% availability during the initial operating period, exceeding the guaranteed 95%. Thermographic inspections after 24 months revealed negligible oxidation degradation where conventional P22 materials historically exhibited scaling after 12 months. The project avoided over €2.7M in potential replacement costs by eliminating planned mid-life refurbishments typical with inferior alloys.
Engineering Considerations for Reliable A335 P91 Applications
Successful implementation requires addressing material-specific technical considerations. Weld procedure specifications must integrate controlled interpass temperatures between 200-250°C along with mandatory post-weld heat treatment at 760±14°C. Recent metallurgical research confirms deviations exceeding these parameters cause Type IV cracking susceptibility in heat-affected zones. Design protocols increasingly incorporate finite element modeling that identifies critical stress concentration zones requiring localized wall thickness increases. Industry failure analyses show installations with comprehensive PWHT verification achieve 92% lower premature failure rates versus systems with incomplete thermal processing documentation.
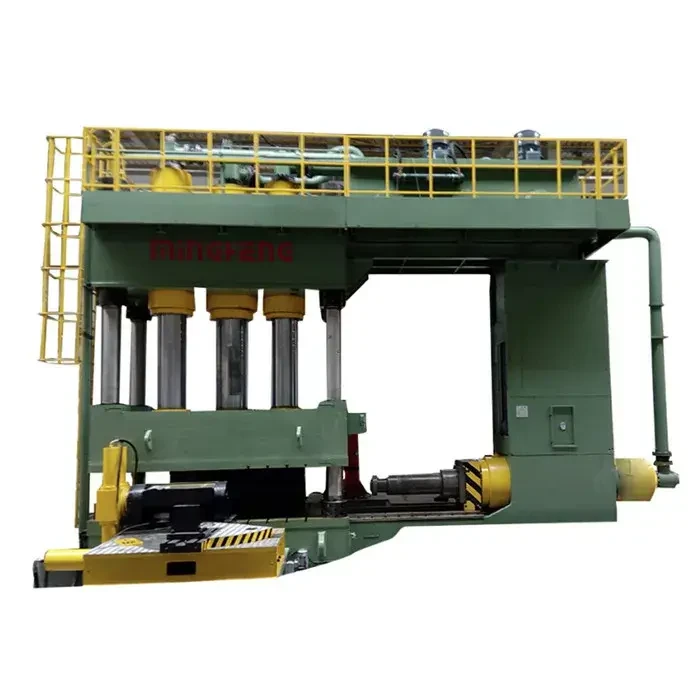
(a335 p91)
FAQS on a335 p91
Q: What is ASTM A335 P91 material?
A: ASTM A335 P91 is a chrome-molybdenum alloy steel pipe for high-temperature service. It offers exceptional creep strength and oxidation resistance. Common uses include power plants and petrochemical systems under high stress.
Q: Where are ASTM A335 P91 pipes typically used?
A: A335 P91 pipes are widely deployed in boilers, steam lines, and superheaters in thermal power stations. They handle steam temperatures exceeding 538°C (1000°F) in critical applications like refineries and chemical plants.
Q: What temperature range suits ASTM A335 P91 pipes?
A: ASTM A335 P91 pipes operate reliably from -20°F to 1200°F (-29°C to 650°C). Their elevated temperature capabilities make them ideal for sustained high-pressure steam service. Avoid prolonged use above 650°C to prevent microstructural degradation.
Q: Why choose A335 P91 over other pipe materials?
A: A335 P91 outperforms lower-grade steels with superior tensile strength and creep resistance at 600°C+. This reduces piping thickness by 30-50% versus P22 steel, cutting costs. Its chrome-moly composition also resists thermal fatigue better than carbon steels.
Q: What are key welding requirements for ASTM A335 P91 pipe?
A: Welding ASTM A335 P91 requires preheating to 400-450°F and strict post-weld heat treatment at 1350-1470°F. Matching P91 filler metals and controlled interpass temperatures are mandatory to prevent cracking. PWHT holds for minimum 1 hour per inch of thickness.
Post time: Jun . 03, 2025 22:37