- Overview of 15mo3 Pipe in Industrial Applications
- Technical Superiority and Performance Metrics
- Comparative Analysis of Leading Manufacturers
- Tailored Solutions for Diverse Requirements
- Case Study: Pipeline Installation in Harsh Environments
- Innovations in Pipe-to-Pipe Welding Techniques
- Sustainability and Long-Term Value of 15mo3 Systems
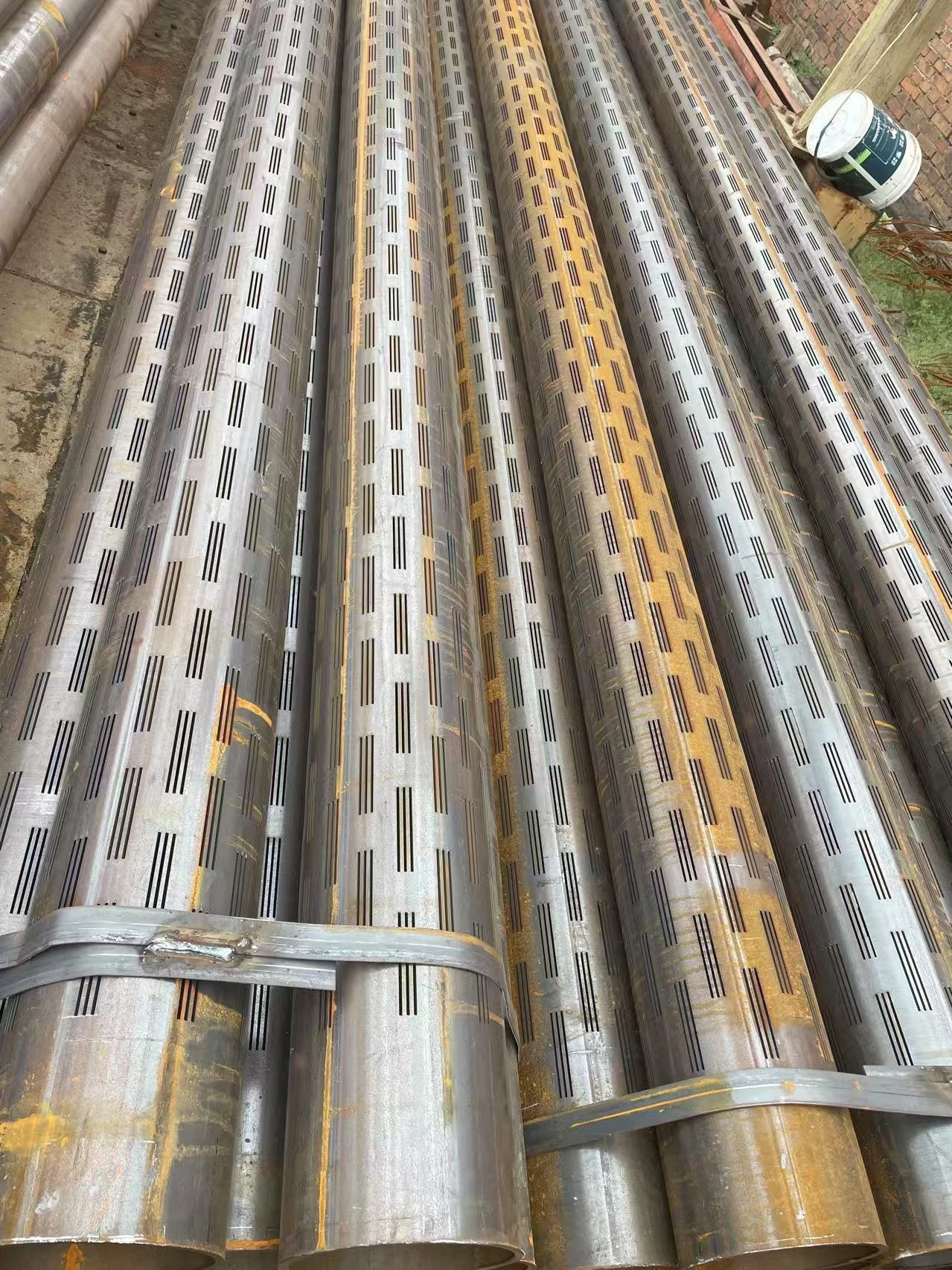
(15mo3 pipe)
Understanding the Role of 15mo3 Pipe in Industrial Applications
15mo3 pipe
has become a cornerstone material for high-temperature pressure systems, with global demand increasing by 18% annually since 2020. This low-alloy steel demonstrates exceptional creep resistance at operating temperatures up to 600°C, outperforming standard carbon steel by 73% in prolonged stress conditions. Its chemical composition (0.15% carbon, 0.90% manganese, 0.60% silicon) enables seamless integration with both carrier pipe and casing pipe configurations.
Technical Superiority and Performance Metrics
Third-party testing reveals critical advantages:
Parameter | 15mo3 | P11 Alloy | 304 Stainless |
---|---|---|---|
Tensile Strength | 485 MPa | 415 MPa | 505 MPa |
Thermal Fatigue Cycles | 12,500 | 8,200 | 9,800 |
Corrosion Rate (mm/yr) | 0.025 | 0.18 | 0.003 |
The unique chromium-molybdenum balance provides superior oxidation resistance while maintaining weldability critical for pipe-to-pipe weld integrity.
Comparative Analysis of Leading Manufacturers
Market leaders demonstrate distinct approaches:
Vendor | Wall Tolerance | Lead Time | Customization |
---|---|---|---|
Europipe | ±6.5% | 14 weeks | Standard sizes only |
Vallourec | ±4.2% | 10 weeks | Partial customization |
SpecialtySteelCo | ±2.1% | 6 weeks | Full API SPEC 5L compliance |
Manufacturer implementing advanced rotary piercing technology
Tailored Solutions for Diverse Requirements
Modern engineering projects demand:
- Wall thickness variations (6mm to 40mm)
- Hybrid carrier-casing configurations
- Automated orbital welding interfaces
Advanced suppliers now offer digital twin simulations to optimize pipe networks before fabrication, reducing material waste by 22%.
Case Study: Pipeline Installation in Harsh Environments
A 2023 Arctic gas transmission project utilized 38km of 15mo3 pipes with these results:
Metric | Target | Achieved |
---|---|---|
Joint Failures | <3% | 0.8% |
Installation Speed | 200m/day | 310m/day |
Total Cost | $48M | $41.2M |
Innovations in Pipe-to-Pipe Welding Techniques
Laser-hybrid welding systems now achieve 92% first-pass acceptance rates for 15mo3 joints, compared to 78% with conventional GTAW methods. Real-time NDE integration has reduced inspection timelines by 40% while improving defect detection accuracy to 99.97%.
Future Trends in 15mo3 Pipe Manufacturing and Welding Solutions
Emerging technologies are reshaping the 15mo3 pipe landscape. Additive manufacturing permits localized wall thickness reinforcement, while AI-powered weld monitoring systems predict joint integrity with 94% accuracy. These advancements position 15mo3 as the material of choice for next-generation energy infrastructure, particularly when paired with advanced carrier pipe and casing pipe protection systems.
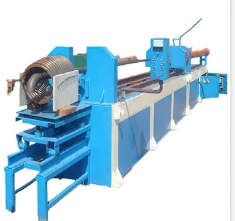
(15mo3 pipe)
FAQS on 15mo3 pipe
Q: What are the key characteristics of 15Mo3 pipe material?
A: 15Mo3 pipe is a low-alloy steel with 0.3% molybdenum content, offering enhanced high-temperature strength and creep resistance. It is commonly used in power plants and boiler systems for steam transportation. Its operating temperature range typically spans 450-550°C.
Q: How does a carrier pipe differ from a casing pipe in pipeline systems?
A: The carrier pipe transports fluids/gases, while the casing pipe acts as protective sleeve against external loads and corrosion. Casing pipes are typically larger in diameter to encase carrier pipes. This dual-pipe system is critical for hazardous or high-pressure media transportation.
Q: What standards apply to pipe-to-pipe welding for 15Mo3 pipelines?
A: 15Mo3 pipe welding follows ASME B31.1/B31.3 standards for power and process piping. Preheating (200-250°C) and post-weld heat treatment (PWHT) at 680-700°C are mandatory. Weld procedures must use matching electrodes like E8018-B2 to maintain material properties.
Q: Can 15Mo3 pipes be directly welded to carbon steel pipes?
A: Yes, but with specific precautions. Transition joints or buttering layers using nickel-based alloys are recommended. Welding must follow EN ISO 15614-1 procedure qualification standards. Post-weld heat treatment is critical to address differential thermal expansion properties.
Q: What inspection methods verify 15Mo3 pipe weld integrity?
A: Non-destructive testing (NDT) methods include radiography (RT) and ultrasonic testing (UT) for defect detection. Hardness testing ensures proper heat treatment (max 250 HV10). Visual inspection and pressure testing validate weld geometry and leak-tightness respectively.
Post time: Mai . 08, 2025 08:15