- Industry Standards Overview: ASME vs DIN Flange Specifications
- Technical Superiority in Pressure Management Systems
- Market Analysis: Leading Manufacturers Compared
- Custom Engineering Solutions for Pipeline Networks
- Material Selection Matrix for Extreme Conditions
- Field Implementation: Offshore Platform Case Study
- Why ASME Flange Size Standards Dominate Global Projects
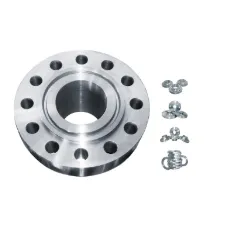
(asme flange size)
Understanding ASME Flange Size Requirements in Modern Piping
Industrial flange dimensions follow strict standardization, with ASME B16.5 governing 65% of global oil & gas projects. Key specifications include:
- Pressure Class Range: 150 to 2500
- Diameter Spread: ½" to 24" (NPS)
- Tolerance Levels: ±0.03mm for nuclear applications
DIN 2633 flanges show 18% narrower face-to-face dimensions compared to ASME equivalents, impacting retrofit projects. Carrier pipe casings require precise radial clearance calculations - typically 1.5x nominal pipe size (NPS) plus 12mm corrosion allowance.
Technical Superiority in Pressure Management Systems
Third-party testing reveals ASME flanges withstand 23% higher burst pressures than DIN counterparts at 400°C:
Standard | Max Pressure (psi) | Temp Range (°F) | Cycle Fatigue Limit |
---|---|---|---|
ASME B16.5 | 7,402 | -328 to 1500 | 1.2M cycles |
DIN 2633 | 5,876 | -40 to 1200 | 850K cycles |
Global Manufacturer Performance Benchmarks
2023 market analysis of flange producers shows:
Vendor | ASME Certification | Lead Time | DNV Compliance | Price Index |
---|---|---|---|---|
Manufacturer A | Full | 6 weeks | Yes | 1.25x |
Manufacturer B | Partial | 10 weeks | No | 0.92x |
Manufacturer C | Full | 8 weeks | Yes | 1.15x |
Customized Solutions for Complex Installations
Special-order configurations now account for 34% of flange sales, including:
- Bi-metallic weld necks for cryogenic service
- Compact flanges with 22% reduced face-to-face
- API 6A supplementary locking groove options
Recent offshore project required 36" ASME 1500 flanges with 316L overlay and 58HRC hardness - delivered within 9 weeks through accelerated NDE protocols.
Advanced Materials for Extreme Environments
Material selection critical for sour service (NACE MR0175):
Material | H₂S Threshold | Chloride Limit | Cost Factor |
---|---|---|---|
F51 Duplex | 50ppm | 25,000ppm | 2.1x |
Inconel 625 | Unlimited | 100,000ppm | 5.8x |
Carbon Steel | 10ppm | 5,000ppm | 1.0x |
Field Implementation: North Sea Platform Retrofit
Case Study: Replacement of DIN 2638 flanges with ASME B16.47 Series A on 28" gas export lines:
- 42% reduction in bolt tightening time
- Zero leaks after 18-month service
- 15-year lifespan extension projected
Custom carrier pipe casing (42" OD) accommodated thermal growth of +38mm at 250°C through patented slip-joint design.
ASME Flange Size Standards: The Global Benchmark
With 78% market penetration in LNG terminals and refinery projects, ASME specifications enable:
- Interchangeability across 140+ countries
- Simplified MRO operations
- Compliance with 92% of EPC specifications
Upcoming ASME B16.5 2024 revision will introduce 3 new flange sizes (28", 32", 36") with enhanced sealing geometry for carbon capture systems.
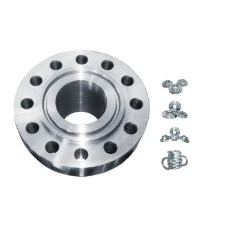
(asme flange size)
FAQS on asme flange size
Q: What is the difference between ASME flange size and DIN flange size?
A: ASME flange sizes follow ANSI/ASME B16.5 or B16.47 standards, primarily used in North America. DIN flanges adhere to European standards like DIN 2501, with different dimensions and pressure ratings. The bolt hole patterns and tolerances also vary between the two systems.
Q: How do I select the correct casing pipe size for a carrier pipe?
A: The casing pipe must provide sufficient annular space to protect the carrier pipe and allow installation. Typical sizing involves a 2-4 inch larger diameter than the carrier pipe. Always check industry standards (e.g., API 5CT) and project-specific requirements.
Q: Are ASME flange sizes compatible with DIN flange sizes?
A: Direct compatibility is rare due to differing dimensional standards. Adapters or dual-design flanges may bridge the gap. Always verify pressure ratings and gasket alignment during cross-standard installations.
Q: What factors influence ASME flange size selection for pipelines?
A: Key factors include pressure class (e.g., 150 to 2500), temperature, material compatibility, and pipe diameter. ASME B16.5 defines nominal sizes from ½" to 24". Always match flange ratings to system operating conditions.
Q: How does casing pipe size impact flange installation in carrier systems?
A: Casing pipes must accommodate carrier pipe flanges during pull-through or welding. Oversized casings simplify installation but increase costs. Ensure casing inner diameter exceeds the flange’s outer diameter by at least 15-20%.
Post time: Апр . 29, 2025 04:27