- Introduction to Heat Exchanger Tube Materials
- Technical Superiority: Titanium vs Stainless Steel
- Performance Metrics Comparison
- Determining Shell and Tube Configuration Parameters
- Custom Engineering Solutions
- Industrial Application Case Studies
- Selecting Titanium Tubes for Heat Exchanger Efficiency
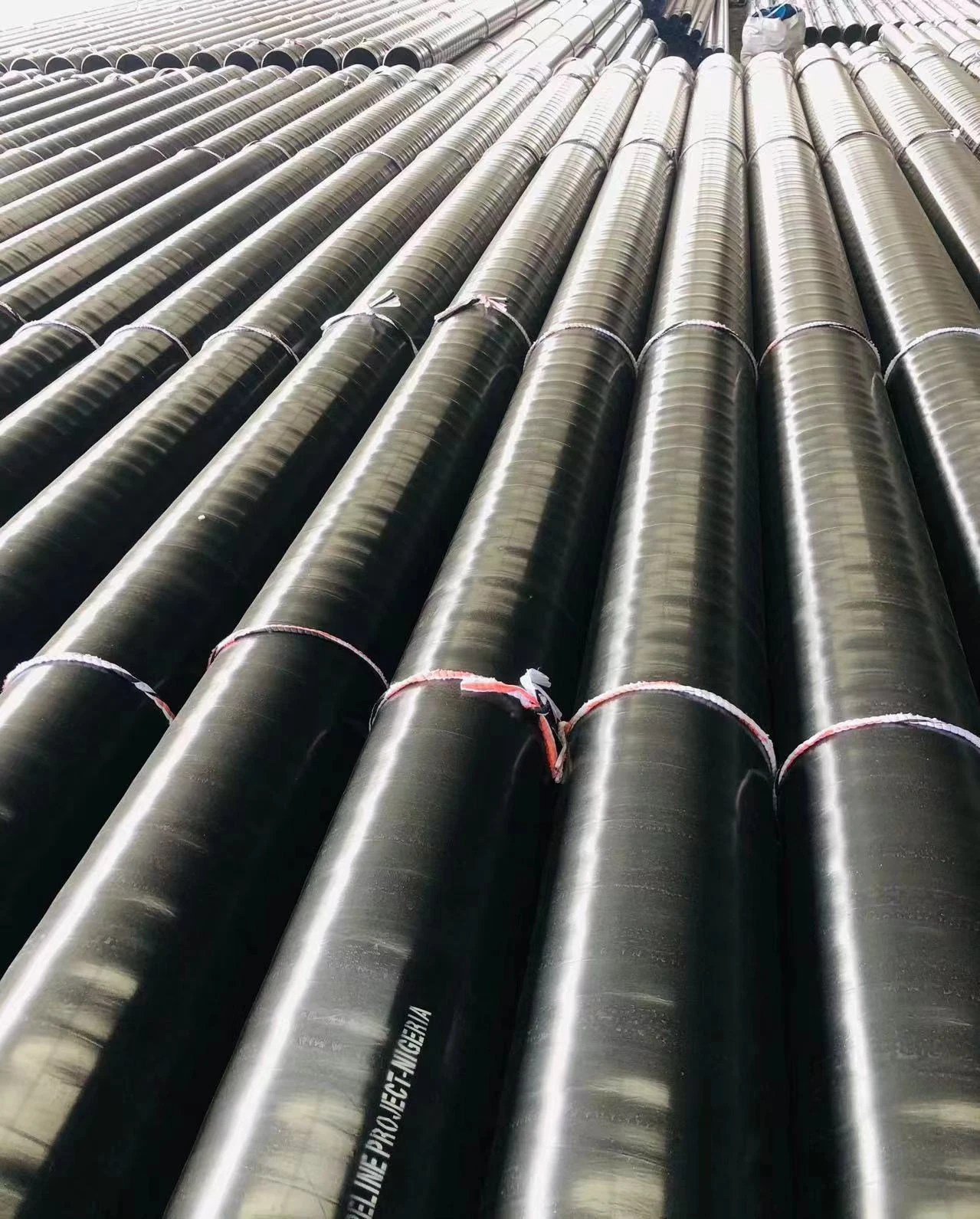
(titanium tubes for heat exchanger)
Understanding the Critical Role of Titanium Tubes for Heat Exchanger Systems
Modern thermal management relies heavily on advanced heat exchange systems across power generation, chemical processing, and maritime industries. Titanium tubes for heat exchanger applications represent a premium solution where standard stainless steel alternatives encounter limitations. The aerospace-grade metal provides unparalleled reliability in corrosive environments like seawater cooling systems where salt concentration accelerates chloride stress cracking. Industry reports confirm titanium heat exchanger tubing lasts 3-5x longer than 316L stainless steel in marine applications, reducing replacement cycles from 2 years to 7+ years according to Petrochem maintenance logs.
Technical Advantages in Extreme Operating Environments
Titanium's technical superiority originates from its passive oxide layer that self-repairs upon damage, creating permanent corrosion resistance absent in reactive metals. This property proves indispensable when handling chlorides, acids, or alkaline fluids above 60°C. Titanium tubes maintain tensile strength exceeding 240 MPa even at 300°C operating temperatures where stainless steel experiences significant creep deformation. Additionally, thermal conductivity ratings reach 21 W/(m·K) with wall thicknesses 20% thinner than equivalent stainless tubes – enabling more compact exchanger designs without compromising heat transfer coefficients.
Parameter | Titanium Gr.2 | 316L Stainless |
---|---|---|
Corrosion Rate in Seawater (mm/year) | <0.0025 | 0.12 |
Maximum Continuous Service Temp (°C) | 316 | 260 |
Thermal Conductivity (W/m·K) | 21 | 16 |
Fatigue Strength (MPa) | 480 | 240 |
Lifetime in Offshore HX (years) | 12-15 | 4-7 |
Optimizing Shell and Tube Heat Exchanger Configurations
Determining the optimal shell and tube heat exchanger number of tubes requires balancing thermal duty parameters against pressure drop constraints. For titanium-based designs, maximum tube counts typically range between 50-10,000 depending on shell diameters from 8" to 60". ASME recommendations suggest maintaining tube-to-baffle clearances of 0.8mm and limiting fluid velocity to 4 m/s to prevent erosion-corrosion in seawater applications. Computational simulations show titanium's higher strength permits thinner 0.5mm walls versus stainless steel's 0.9mm minimum, increasing tube count density by 28% within identical shell dimensions while enhancing overall surface area efficiency.
Customized Tubing Solutions for Complex Requirements
Manufacturers now offer engineered titanium tubing solutions addressing specific operational challenges beyond standard ASTM B338 grades. For high-pressure steam applications above 50 bar, seamless cold-drawn titanium tubes undergo rotary expanding to achieve precise 25.4mm ±0.05mm diameters. Specialized annealing processes enhance formability for U-bend designs achieving 2D bend radii without wall thinning. For severely fouling media, electrophoresis-coated titanium tubes with 15µm PTFE layers reduce particulate adhesion by 80% while maintaining thermal transfer characteristics within 5% of bare tube performance.
Industrial Implementation Success Stories
Offshore platform cooling systems witnessed transformational results after transitioning to titanium tubing. An Equinor processing platform reported 34% lower maintenance costs and zero tube failures across 5 years of service. Similar outcomes emerged in chemical processing: DuPont's HCl purification unit extended run cycles from 11 months to 4.2 years after adopting welded titanium tubes. Perhaps most notably, flue gas desulfurization scrubbers in coal plants recorded heat transfer improvements of 14% when replacing super-austenitic stainless tubes with thin-wall titanium alternatives, demonstrating how material selection directly impacts operational thermodynamics beyond corrosion management.
Future-Proofing Systems with Titanium Tubes for Heat Exchanger Design
Specifying titanium tubes for heat exchanger
systems delivers compounding operational advantages extending beyond initial capital investment. With total lifecycle costs proven 17-22% lower than specialty stainless alloys in decade-long industrial studies, the metallurgical investment creates predictable long-term value. Recent material science breakthroughs like Grade 19 titanium alloys push temperature thresholds to 425°C while maintaining corrosion immunity, potentially expanding application envelopes to nuclear and geothermal sectors. As operational demands intensify across energy-intensive industries, titanium's unique properties continue redefining performance boundaries for next-generation thermal management solutions.
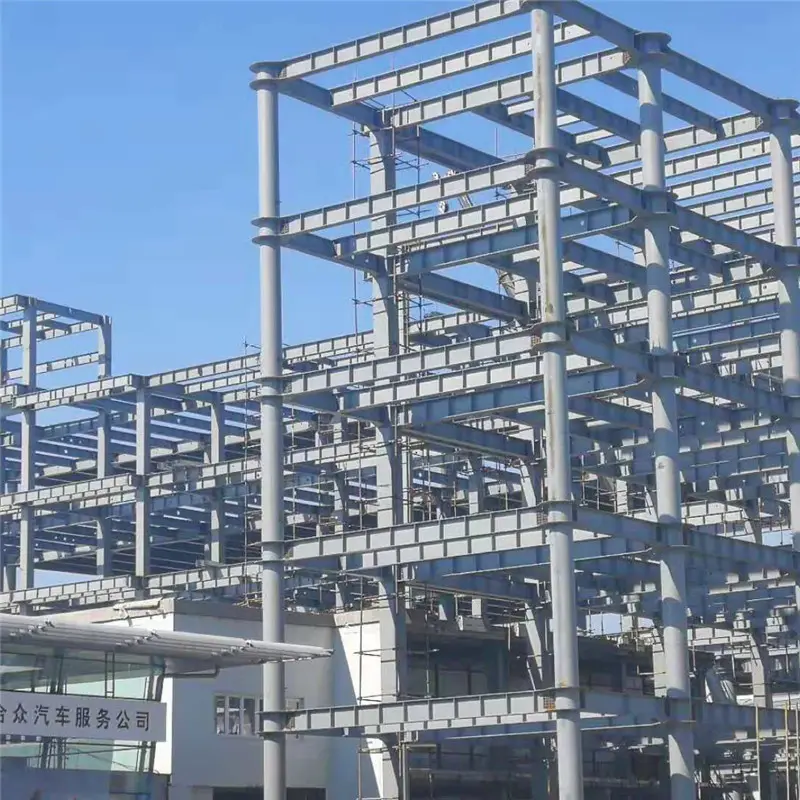
(titanium tubes for heat exchanger)
FAQS on titanium tubes for heat exchanger
Q: What are the key advantages of titanium tubes in heat exchangers?
A: Titanium tubes offer exceptional corrosion resistance against seawater and chemicals, doubling lifespan versus steel. They provide high thermal conductivity for efficient heat transfer while remaining lightweight. This makes them ideal for aggressive environments like marine applications.
Q: How do titanium tubes compare to stainless steel for heat exchanger performance?
A: Titanium surpasses stainless steel in corrosion resistance, especially in chloride-rich environments like offshore operations. Though titanium has slightly lower thermal conductivity than stainless steel, its superior durability often justifies the cost premium. Both materials maintain excellent pressure containment in shell-and-tube configurations.
Q: How is the number of tubes determined in shell and tube heat exchangers?
A: Tube count depends on heat transfer requirements calculated from thermal duty and fluid properties. Engineers optimize tube quantity considering flow velocities (typically 1-3 m/s), pressure drop limits, and available shell diameter. Standard tube layouts (triangular, square) maximize surface area within spatial constraints.
Q: Why choose titanium tubes for seawater-cooled heat exchangers?
A: Titanium withstands seawater's corrosive chlorides and biofouling where stainless steel fails, preventing pitting and crevice corrosion. Its natural oxide layer resists erosion from sand particles in seawater intake. These properties virtually eliminate tube leaks, making titanium the premier choice for desalination and marine systems.
Q: What maintenance considerations apply to titanium heat exchanger tubes?
A: Titanium tubes require minimal maintenance due to non-corrosive properties, reducing cleaning frequency versus steel tubes. Mechanical cleaning must avoid abrasive methods that damage the passive oxide layer. Inspections should verify tube-to-tube sheet joints, as titanium expands differently than carbon steel shells.
Post time: ਜੂਨ . 05, 2025 16:21