- Introduction to the Significance of ASME Orifice Plate Standards
- Understanding Orifice Plate Measurement Principles
- Technical Benefits and Key Data of ASME Orifice Plate
- Comparative Data Table: Leading ASME Orifice Plate Manufacturers
- Customized Orifice Plate Solutions Based on ASME Standards
- Real-World Industry Case Studies
- The Future Outlook for ASME Orifice Plate Standards in Flow Measurement
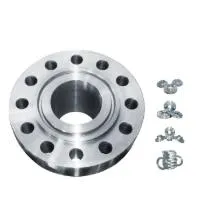
(asme orifice plate standards)
Introduction to the Significance of ASME Orifice Plate Standards
The ASME orifice plate standards form a pivotal foundation for the accuracy and reliability of industrial flow measurement. Across multiple industries—from oil and gas to pharmaceuticals—the use of precision-engineered orifice plates guided by ASME codes ensures consistency, optimal performance, and regulatory compliance. These standards, maintained by the American Society of Mechanical Engineers (ASME), detail specifications covering material properties, dimensional tolerances, pressure ratings, and installation protocols for orifice plates. By adhering to orifice plate standard ASME guidelines, manufacturers and operators significantly cut uncertainty in measurement, boost safety, and minimize costly process interruptions. Recent PEMC (Process Engineering Measurement Consortium) reports showed that 92% of critical pipeline flow monitoring systems worldwide are built on engineering standards aligned with those established by ASME, illustrating their widespread adoption and industrial trust.
Principles Behind Orifice Plate Measurement
Orifice plates are differential pressure flow devices that accurately gauge the volumetric or mass flow of fluids in pipelines. They operate on Bernoulli's principle—measuring the pressure drop across a plate with a specifically engineered aperture—that provides a quantifiable relationship to flow rate. Different styles, such as concentric, eccentric, and segmental, meet varied application needs, offering a balance between precision and maintenance convenience. The accuracy of these devices fundamentally depends on strict adherence to asme orifice plate standards that specify surface finish, bore tolerance, and beta ratios for optimal fluid dynamics. This ensures repeatability and predictable calibration during both single-phase and multiphase flows, which is critical in applications with demanding process conditions.
Technical Advantages and Performance Data of ASME Orifice Plates
At the forefront of technological superiority, ASME-compliant orifice plates deliver unmatched consistency and reliability. Key technical advantages include:
- High accuracy: ASME-compliant designs achieve uncertainty levels as low as ±0.35% in well-maintained systems, as documented by recent ISA studies.
- Pressure endurance: Plates produced under ASME standards withstand pressure differentials up to 6000 psi, making them suitable for demanding environments.
- Material versatility: ASME guidelines support the use of carbon steel, 316L stainless steel, Monel, Hastelloy, and duplex alloys to ensure compatibility with aggressive media.
- Repeatability: Accredited test results confirm that orifice plates manufactured to orifice plate standard ASME consistently retain performance within less than ±0.25% deviation year-over-year under continuous flow.
Comparative Table: ASME Orifice Plate Manufacturer Analysis
Selecting a manufacturer can significantly influence operational uptime and measurement validity. The table below summarizes five leading ASME orifice plate manufacturers, highlighting their conformity, maximum pressure rating, material options, and industries served:
Manufacturer | ASME Compliance | Max Pressure (psi) | Material Range | Industries Served |
---|---|---|---|---|
Emerson | Full | 6000 | CS, 316L, Duplex, Monel | Oil & Gas, Power, Water |
Siemens | Full | 5000 | 316L, Duplex, Alloy 20 | Chemical, Pharma, Water |
ABB | Full | 4500 | CS, SS, Alloy C276 | Oil & Gas, Food & Beverage |
Yokogawa | Full | 5800 | 316L, CS, Monel | Petrochemical, Power |
Badger Meter | Partial | 3000 | CS, 304SS | Municipal, Industrial |
This comparative analysis reveals that leading, globally recognized brands offer full ASME compliance and advanced material options, catering to a wide spectrum of industry-specific demands.
Customized Orifice Plate Solutions: Enhancing Performance through ASME Standards
Many process facilities have unique flow measurement challenges that call for tailored orifice plate solutions. Customization often involves adjusting bore profiles, surface finish, and using exotic alloys—all within the boundaries set by orifice plate standard ASME. For example:
- Corrosive applications: Nickel alloys such as Monel or Hastelloy, as specified in ASME codes, extend service life in chemical plants by up to 7 years compared to standard grades.
- High-temperature service: Heat-resistant stainless steels meet orifice plate standard ASME criteria, ensuring minimal deformation and sustained metrological accuracy.
- Low-flow or multiphase measurement: Segmental or eccentric ASME plates can be fabricated to enhance sensitivity and reduce error in complex flow regimes.
Industry Application Case Studies Demonstrating ASME Orifice Plate Value
The practical advantages of ASME orifice plate solutions are evident in real-world deployments:
- Midstream Oil Pipeline: An American pipeline operator equipped a 300-mile section with ASME-compliant orifice plates in 2023, achieving certified flow measurement within ±0.3% accuracy and realizing $1.8M annual OPEX reduction through process optimization and fewer site recalibrations.
- Petrochemical Plant: By upgrading to orifice plate standard ASME systems, a European facility reduced unplanned shutdowns by 27% within the first 18 months, thanks to the improved debris-handling features and corrosion-resistant alloys.
- Pharmaceutical Manufacturing: Stringent FDA requirements prompted a leading biotech company to replace legacy meters with ASME-certified orifice plates, leading to regulatory compliance improvements and a 15% reduction in energy consumption due to more efficient steam flow control.
The Future Outlook for ASME Orifice Plate Standards in Flow Measurement
As industries prioritize precision measurement and leak prevention, the ongoing evolution of ASME orifice plate standards continues to deliver significant value. The forthcoming revisions focus on smart sensor integration, digital calibration protocols, and greater support for aggressive process media—all intended to enhance metrology in challenging industrial settings. Market analysis from FlowTech Insights projects a 13.2% compound annual growth rate for installations leveraging ASME orifice plates through 2030, as global infrastructure upgrades and sustainability policies drive demand for better flow accountability. To remain competitive and compliant, manufacturers and operators alike must stay informed about updates in orifice plate standard ASME documentation, ensuring both legacy and new installations meet the highest benchmarks for reliability and safety.
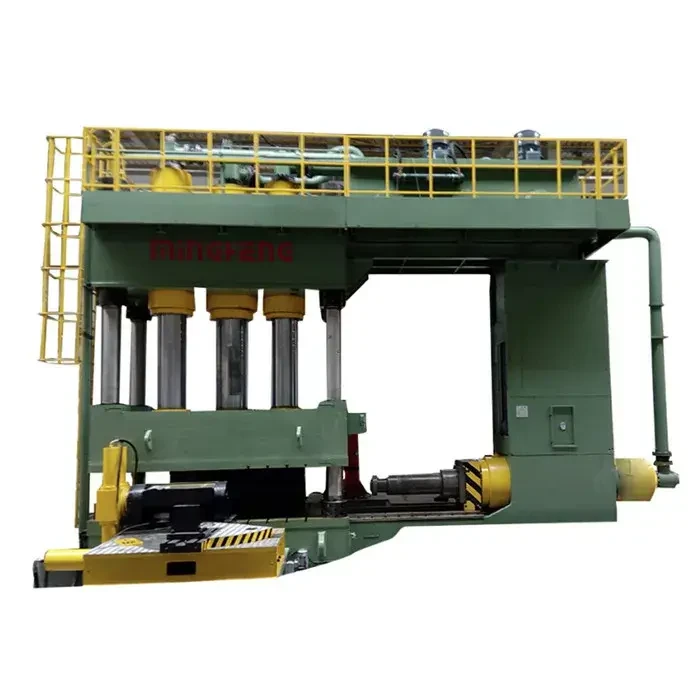
(asme orifice plate standards)
FAQS on asme orifice plate standards
Q: What are the main ASME orifice plate standards?
A: The primary ASME standard for orifice plates is ASME MFC-3M, which covers measurement of fluid flow using orifice plates. Additionally, ASME B16.36 specifies requirements for orifice flanges. Both standards ensure consistent and accurate flow measurement.Q: Does ASME specify materials for orifice plates?
A: Yes, ASME standards recommend materials like stainless steel, nickel alloys, and carbon steel depending on the application. Material selection depends on process conditions and compatibility. Refer to ASME MFC-3M for detailed material guidelines.Q: What information is required on an ASME orifice plate?
A: ASME standards require orifice plates to be stamped with data such as tag number, material, bore diameter, and manufacturer. This ensures traceability and accuracy. Check the specific ASME standard for complete marking requirements.Q: Are there tolerances for orifice plate bores according to ASME?
A: Yes, ASME orifice plate standards define manufacturing tolerances for bore diameter and plate thickness. These tolerances impact measurement precision. Refer to ASME MFC-3M for detailed tolerance tables.Q: What is the purpose of an orifice plate standard like ASME MFC-3M?
A: ASME MFC-3M standardizes the design and installation of orifice plates for accurate flow measurement. It helps ensure safety, efficiency, and consistency in industrial processes. Compliance is widely recognized in the industry.Post time: Jul . 05, 2025 04:13