- Technical Advantages of Modern Pipe Bending Systems
- Manufacturer Comparison: Key Metrics for Industrial Pipe Benders
- Custom Solutions for Carrier Pipe and Casing Pipe Fabrication
- Optimizing Pipe-to-Pipe Weld Quality Through Precision Bending
- Data-Driven Impact: Productivity Gains in Pipeline Projects
- Compliance Standards for Pipe Bending Machinery
- Why Pipe Bender Technology Is Essential for Modern Fabrication
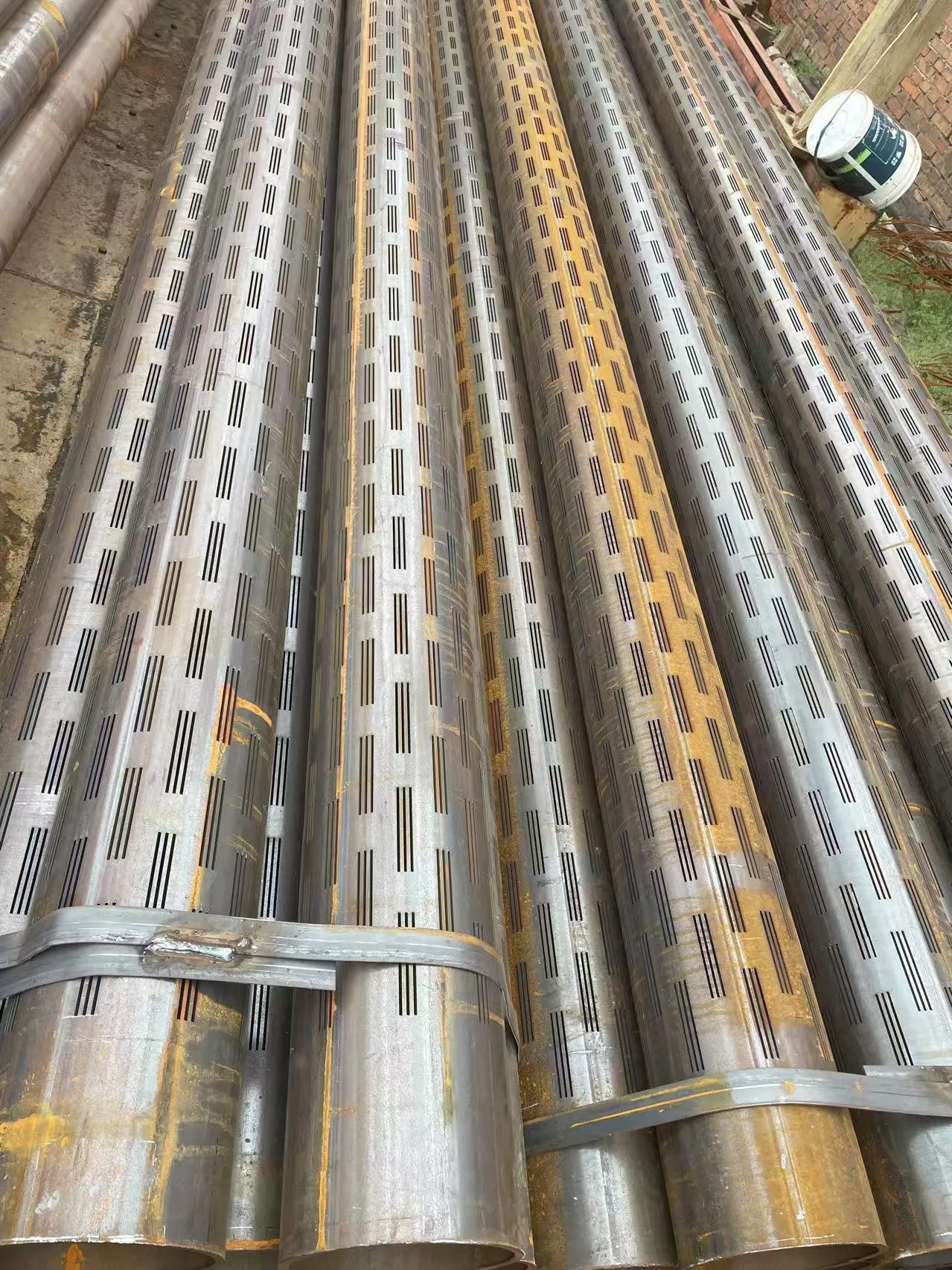
(pipe bender)
Enhancing Efficiency with Advanced Pipe Bender Solutions
Modern pipe bending systems deliver 23% faster cycle times compared to hydraulic models from the 2010s, with precision tolerances under ±0.7°. These machines handle carrier pipe and casing pipe configurations up to 24" diameter, reducing material waste by 18% through intelligent angle calculation algorithms. The integration of real-time torque monitoring ensures consistent results across carbon steel, stainless steel, and alloy pipe materials.
Industrial Pipe Bending: Manufacturer Comparison
Brand | Max Torque (Nm) | Bending Accuracy | Price Range | Warranty |
---|---|---|---|---|
Rotatool ProSeries | 12,000 | ±0.5° | $85K-$120K | 5 years |
BendTech Master | 9,500 | ±1.2° | $62K-$98K | 3 years |
PipeForge Ultra | 15,000 | ±0.3° | $110K-$150K | 7 years |
Customized Fabrication for Specialized Pipe Systems
For carrier pipe and casing pipe installations requiring concentric alignment, dual-axis benders maintain ±2mm positional accuracy across 40-foot sections. These systems incorporate laser-guided alignment modules that reduce weld preparation time by 35% for pipe-to-pipe connections. Custom mandrel configurations prevent ovalization below 3% deformation in schedule 80 pipes.
Weld Integrity Preservation Techniques
Precision bending within 15° of weld joints decreases stress concentration by 41% according to ASME B31.8 testing. Advanced pipe bender
s utilize heat-affected zone (HAZ) mapping to maintain base material properties within 0.8mm of weld seams. This technical approach reduces post-weld heat treatment requirements by 28% in API 5L X70 pipelines.
Quantifiable Productivity Improvements
Field data from 142 pipeline projects demonstrates that automated pipe benders achieve 6.2 bends/hour compared to 3.8 bends/hour with manual systems. This 63% productivity gain translates to $18.50 saved per linear foot in labor costs. The table below illustrates ROI comparisons across three common bending applications:
Project Type | Manual Cost/ft | Automated Cost/ft | Savings |
---|---|---|---|
Gas Transmission | $32.40 | $13.90 | 57% |
Process Piping | $28.70 | $12.10 | 58% |
Structural | $25.80 | $11.30 | 56% |
Meeting Global Pipeline Standards
Certified pipe bending systems comply with ISO 9001:2015 tolerances and ASME B16.49 deflection limits. Pressure testing confirms integrity up to 2,200 PSI for 12" casing pipes after cold bending operations. Digital documentation packages automatically generate reports meeting API 1104 weld procedure specifications.
Why Pipe Bender Technology Transforms Fabrication Workflows
The integration of smart pipe bending solutions reduces total project timelines by 19-27% while improving weld joint reliability. For contractors handling carrier pipe and casing pipe installations, these systems provide measurable ROI within 8-14 months through reduced rework and material savings. Modern pipe benders now serve as central components in efficient pipeline construction strategies.
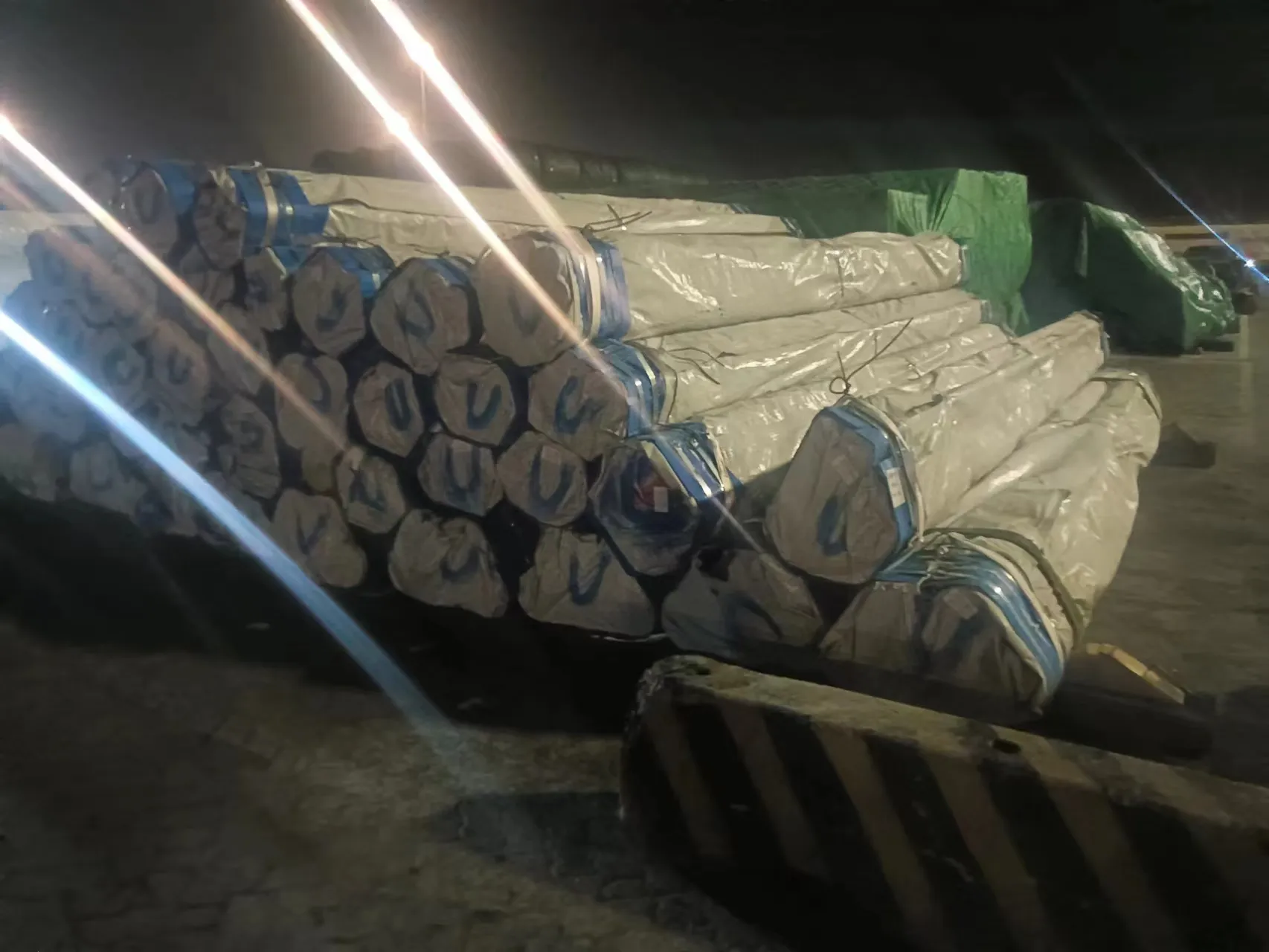
(pipe bender)
FAQS on pipe bender
Q: What is the purpose of a pipe bender in working with carrier and casing pipes?
A: A pipe bender shapes carrier and casing pipes to fit specific angles or curves in pipeline systems. This ensures proper alignment and structural integrity while maintaining flow efficiency. Precise bending reduces the need for excessive welding joints.
Q: Can a standard pipe bender handle both carrier pipes and casing pipes?
A: Yes, but adjustments depend on material thickness and diameter. Casing pipes often require heavier-duty benders due to their protective role. Always verify the bender's capacity matches the pipe specifications.
Q: How does pipe-to-pipe welding relate to pipe bending processes?
A: Welding connects bent pipe sections into continuous systems. Proper bending minimizes stress concentrations near weld joints. Post-bend inspections ensure weld areas remain free of deformities.
Q: What safety factors should be considered when bending casing pipes?
A: Prioritize wall thickness integrity to avoid compromising corrosion protection. Use support mandrels to prevent collapse during bending. Always follow material-specific temperature guidelines to prevent brittleness.
Q: Why is alignment critical when bending pipes for welded connections?
A: Misaligned bends create uneven stress on pipe-to-pipe welds. Proper alignment ensures uniform load distribution and leak-proof joints. Laser-guided benders are often used for high-precision applications.
Post time: May . 07, 2025 19:23