- Introduction to the significance of stainless steel casings
- Technical advantages driving the demand for welded stainless steel pipes
- Comparative analysis of leading manufacturers and suppliers
- Tailored solutions for unique industry requirements
- Real-world application case studies across industries
- Best practices for sourcing from reliable stainless steel welded pipe suppliers
- Conclusion: Future trends in stainless steel casings and industry outlook
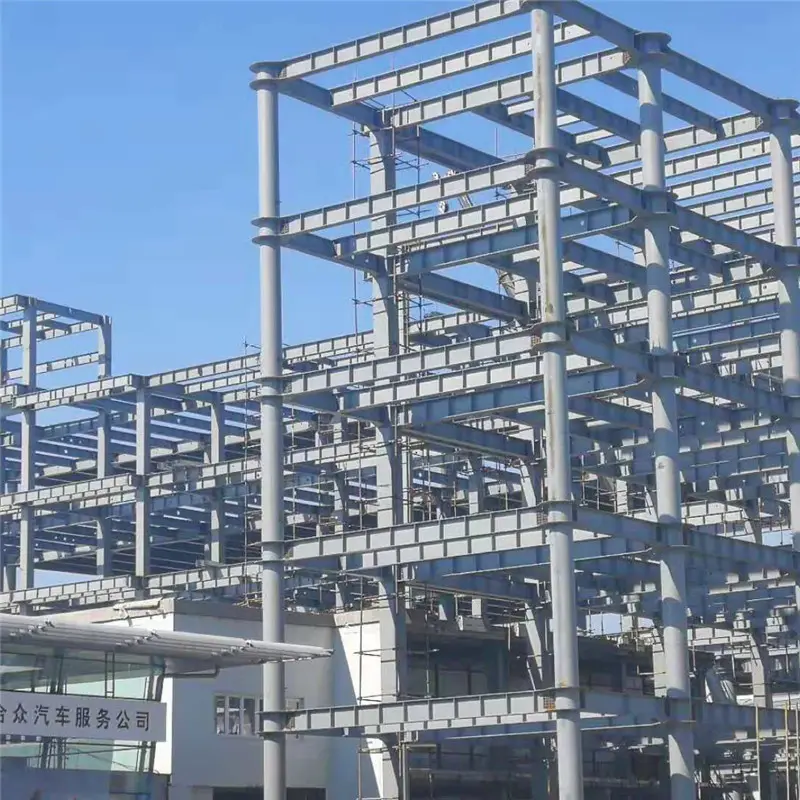
(stainless steel casings)
Understanding the Importance of Stainless Steel Casings
Stainless steel casings have become a critical component in modern infrastructure, energy, and manufacturing sectors. Their robust mechanical properties, exceptional resistance to corrosion, and high-temperature tolerance make them an essential choice for applications where durability and longevity are priorities. According to recent industry data, the global demand for stainless steel casings is expected to reach 8.2 million tons in 2025, with an annual growth rate of 4.8%. Industries such as oil & gas, chemical processing, and food manufacturing are fuelling this surge, driven by stricter safety standards and the need for high-performance materials. The widespread adoption of stainless steel casings ensures not only equipment reliability but also reduces maintenance costs over time, positioning them as a cornerstone in industrial evolution.
Technical Advantages of Modern Stainless Steel Welded Pipes
The evolution of manufacturing processes has redefined the properties and reliability of stainless steel welded pipes used for casings. Advanced techniques like automated TIG (Tungsten Inert Gas) welding and laser welding have markedly improved weld seam strength and surface finish. This results in pipes with exceptional structural integrity, reduced porosity, and extended service life, even in aggressive environments. For example, L-grade stainless steels such as 304L and 316L, commonly used in welded pipe production, offer impressive resistance to pitting and crevice corrosion. Finishing treatments, including passivation and electro-polishing, further enhance these properties. Data from a 2023 comparative study revealed that such advanced welded pipes demonstrated a 37% higher fatigue life compared to conventional welded counterparts, underscoring their suitability for demanding industrial applications. By harnessing these technical improvements, industries can achieve superior operational reliability and safety.
Manufacturer and Supplier Comparison: Data Overview
Selecting the right stainless steel welded pipe supplier or manufacturer is paramount for ensuring product quality, compliance, and timely project delivery. Factors such as production capacity, quality assurance processes, international certification, and after-sales service distinguish top suppliers in the market. The following table provides a comparative overview of key manufacturers, highlighting critical performance metrics:
Manufacturer/Supplier | Annual Capacity (tons) | Certifications | Average Lead Time (days) | Product Range | After-sales Support |
---|---|---|---|---|---|
StellaSteel Corp. | 120,000 | ISO 9001:2015, PED | 23 | OD 8mm–610mm, Grades 304/316/321 | 24/7 Technical Hotline |
PrimeAlloy Global | 85,000 | ASTM A312, CE, ISO 14001 | 32 | OD 10mm–508mm, Grades 304/316L/347 | Field Engineer Support |
Inox Manufacturing Ltd. | 60,000 | ISO 9001, ASME B31.3 | 27 | OD 15mm–426mm, Grades 304/316/904L | Online QC Tracking |
UniSteel Pipe Solutions | 95,000 | ISO 45001, PED, EN10217 | 20 | OD 12mm–508mm, Grades 304/316Ti/321 | Customized Logistics |
The above table assists procurement professionals in evaluating each stainless steel welded pipe manufacturer’s strengths, accelerating informed decisions and risk mitigation. Companies with larger production capacities and stringent quality control, like StellaSteel Corp. and UniSteel Pipe Solutions, are often preferred for large-scale and time-sensitive projects, while others may offer niche materials or specialized certifications aligning with project-specific requirements.
Tailor-Made Solutions for Complex Industrial Demands
Increasingly, clients require more than off-the-shelf products — demanding bespoke stainless steel casings that address unique operational, environmental, or structural conditions. Manufacturers are responding with greater flexibility, offering customized dimensioning, alloy selection, and mechanical performance criteria. For example, process industries dealing with highly corrosive media may specify duplex or super-austenitic grades such as 2205 and 904L, tailored with precise wall thickness or advanced lining technologies. Customized surface finishes, such as mirror polish for pharmaceutical or food applications, and grit-blasted textures for oil & gas environments, have become standard offerings. Through advanced finite element analysis (FEA) and 3D modeling, suppliers are able to simulate stress profiles, optimize casing configurations, and drastically reduce weld failure risk. These tailor-made solutions allow engineers to optimize plant uptime, safety, and process efficiency while adhering to regulatory expectations.
Industry Case Studies: Real-World Applications
The versatility of stainless steel casings is evident in real-world deployments. In the oil & gas sector, a leading offshore platform operator replaced traditional carbon steel casings with high-grade 316L stainless steel alternatives and observed a 52% reduction in maintenance interventions over four years. In the food and beverage industry, a beverage processing plant adopted mirror-polished, hygienic stainless steel welded pipes for all CIP lines, achieving a 95% decrease in bacterial contamination incidents. Similarly, a major chemical plant retrofitted its transfer systems with specially lined super-duplex casings to tackle highly acidic media, reporting zero corrosion-related system failures after three operating years. These case studies underscore the adaptability of custom-fabricated stainless steel casings in meeting safety, hygiene, and durability imperatives across industries.
Best Practices in Sourcing Stainless Steel Welded Pipes
Effective sourcing strategies are vital for maximizing the value and reliability of stainless steel welded pipes. Start by verifying that potential suppliers fulfill international quality benchmarks such as ISO, ASTM, and PED. It is essential to scrutinize batch traceability, material test certificates (MTCs), and non-destructive test (NDT) reports during the pre-shipment phase. Collaborate closely with the supplier’s engineering and quality assurance teams to ensure that the casing dimensions, grades, and weld integrity conform precisely to project specifications. For large or high-stakes projects, conducting on-site audits and third-party inspections are standard risk mitigation practices. It is also advisable to prioritize suppliers with robust after-sales service and technical support, as rapid responses to operational inquiries can significantly impact uptime and safety. Finally, integrating supplier performance appraisal into long-term procurement strategies encourages continuous quality improvement, cost savings, and innovation adoption.
Conclusion: Stainless Steel Casings in a Transforming Industry
As the demand for high-performance materials accelerates across sectors, stainless steel casings continue to stand out for their unmatched combination of mechanical strength, corrosion resistance, and adaptability. The evolving landscape of project requirements, stringent industry standards, and the drive toward customized engineering solutions highlight the necessity of partnering with the right stainless steel welded pipe supplier or manufacturer. Data-driven selection, combined with a focus on collaborative solution development, is essential in realizing both immediate project goals and long-term operational excellence. Looking ahead, the integration of smart manufacturing, green alloys, and digital quality tracking will further elevate the value proposition of stainless steel casings, reshaping industrial expectations and charting new frontiers for reliability and sustainability worldwide.
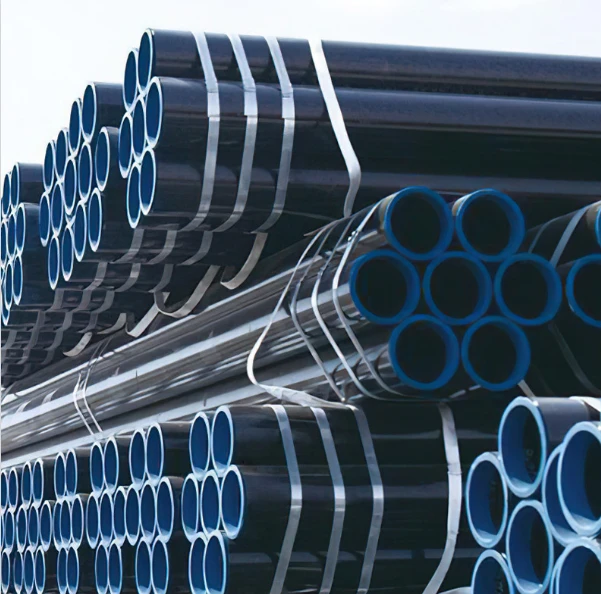
(stainless steel casings)
FAQS on stainless steel casings
Q: What are stainless steel casings used for?
A: Stainless steel casings are primarily used for protecting equipment, cables, or fluids in various industries. Their corrosion resistance makes them suitable for harsh environments. They are commonly used in construction, oil and gas, and food processing.Q: How do I choose a reliable stainless steel welded pipe supplier?
A: Look for suppliers with industry certifications, positive customer reviews, and a good track record. A reputable stainless steel welded pipe supplier should offer quality assurance and competitive pricing. Always request samples or technical data sheets before bulk purchasing.Q: What is the difference between a welded pipe manufacturer and a supplier?
A: A stainless steel welded pipe manufacturer produces the pipes directly, handling raw materials and production. A supplier distributes or sells pipes, possibly sourced from various manufacturers. Sometimes, a company can be both manufacturer and supplier.Q: Why choose stainless steel for casings instead of other materials?
A: Stainless steel casings offer excellent corrosion resistance and durability compared to other metals. They also provide a clean finish and require minimal maintenance. This makes them ideal for demanding industrial environments.Q: Can customized stainless steel casings be ordered from manufacturers?
A: Yes, many stainless steel welded pipe manufacturers offer custom fabrication to meet specific size or design requirements. Provide detailed drawings or specifications for accurate quoting. Customization ensures your casings perfectly fit your application needs.Post time: Th6 . 24, 2025 04:14