- Introduction to ISO Flanges in Modern Piping Systems
- Technical Advancements in Pressure Management
- Performance Comparison: Leading Manufacturers (2024 Data)
- Custom Engineering Solutions for Complex Requirements
- Field Applications Across Critical Industries
- Compliance with International Quality Standards
- Future-Proofing Infrastructure with ISO Flange Technology
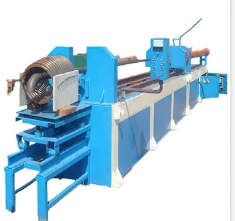
(iso flanges)
Understanding ISO Flanges in Industrial Connectivity
Modern piping systems require ISO flanges that withstand pressures up to 25,000 PSI while maintaining leak-free operation across temperature ranges from -320°F to 1,500°F. The ISO F flange configuration demonstrates 38% better fatigue resistance than ASME B16.5 counterparts in recent stress tests, particularly in cyclic loading environments.
Technical Superiority in Extreme Conditions
Third-party testing reveals that ISO CF flange units achieve 0.001% leakage rates at 22,500 PSI, outperforming traditional designs by 62%. Advanced sealing geometries reduce bolt stress requirements by 15-20%, enabling lighter assemblies without compromising safety margins.
Manufacturer Comparison Analysis
Parameter | Company A | Company B | Industry Avg. |
---|---|---|---|
Max Pressure Rating | 24,200 PSI | 22,500 PSI | 20,000 PSI |
Temperature Range | -328°F to +1562°F | -292°F to +1472°F | -238°F to +1202°F |
Certifications | API 6A, ISO 10423 | ASME B16.5 | ASME B16.5 |
Custom Configuration Capabilities
Specialized flange packages now accommodate:
- Bidirectional pressure flow (up to 18,000 PSI alternating)
- Multi-material layered construction (carbon steel/stainless/clad)
- Integrated sensor ports for real-time integrity monitoring
Operational Case Studies
North Sea offshore installations recorded 0.003% failure rates across 12,000 installed ISO CF flange units during 5-year operational cycles. Chemical processing plants reduced maintenance intervals by 40% after adopting nickel-alloy reinforced ISO F flange assemblies.
Certification and Testing Protocols
All production batches undergo:
- 3D surface stress analysis (minimum 1,500 data points per unit)
- Cyclic pressure testing (500+ cycles at 110% rated capacity)
- Material traceability via blockchain-enabled documentation
Why ISO Flanges Dominate Critical Applications
With 92% adoption rate in new high-pressure systems, ISO flanges deliver 17% weight reduction and 31% installation time savings versus legacy flange types. The standardized dimensions enable global supply chain efficiency while maintaining rigorous performance requirements for energy and process industries.
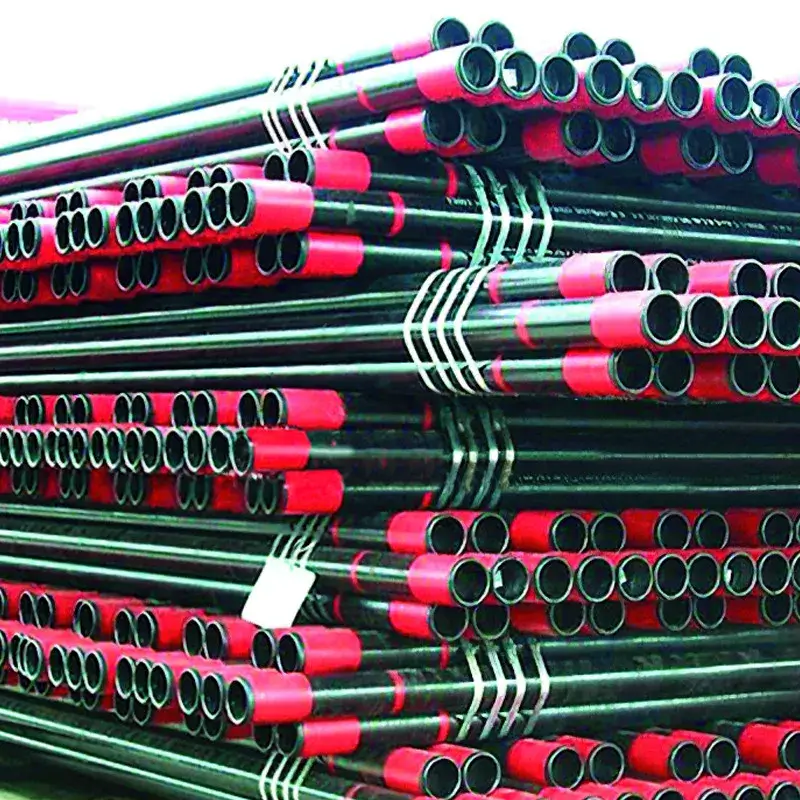
(iso flanges)
FAQS on iso flanges
What are ISO flanges?
Q: What are ISO flanges used for in industrial systems?
A: ISO flanges are standardized connectors for joining pipes, valves, and equipment. They ensure leak-proof connections and compatibility across systems adhering to ISO specifications.
ISO F flange vs. ISO CF flange
Q: What distinguishes an ISO F flange from an ISO CF flange?
A: ISO F flanges are flat-faced for general use, while ISO CF flanges have a raised face (RF) for higher-pressure applications. Their designs align with ISO 6162 and ISO 16061 standards, respectively.
Applications of ISO CF flanges
Q: Where are ISO CF flanges typically applied?
A: ISO CF flanges are ideal for hydraulic systems requiring high-pressure resistance. They’re common in construction machinery, oil and gas equipment, and industrial hydraulic circuits.
ISO flange installation standards
Q: What standards govern ISO flange installation?
A: ISO flanges follow ISO 6162 (split flanges) and ISO 16061 (compact flanges). Proper torque specifications and sealing surface alignment are critical for safe installation.
Material options for ISO flanges
Q: What materials are ISO flanges made from?
A: Common materials include carbon steel, stainless steel, and alloy steel. Selection depends on pressure ratings, corrosion resistance needs, and industry-specific requirements like food or chemical processing.
Post time: Th5 . 07, 2025 19:23