Stainless Pipe Welding Techniques and Importance
Welding stainless steel pipes is a crucial process in a variety of industries, including construction, manufacturing, and energy. This durable and corrosion-resistant material is favored in applications where hygiene and longevity are paramount. Understanding the techniques and best practices associated with stainless pipe welding can significantly improve the integrity and performance of welded joints.
Understanding Stainless Steel
Stainless steel is an alloy that contains a minimum of 10.5% chromium, which gives it its reactive properties that prevent rust and corrosion. The different grades of stainless steel, such as 304 and 316, have varying compositions that influence their properties, making them suitable for specific applications. For instance, type 316 contains molybdenum, which enhances its resistance to chlorides and is ideal for marine environments.
Importance of Proper Welding Techniques
Welding stainless steel pipes requires specific techniques to maintain the material's inherent properties. Improper welding can lead to issues such as distortion, corrosion, and compromise of mechanical strength. Therefore, understanding the various welding methods and their implications is crucial for achieving high-quality welds.
Common Welding Techniques
1. TIG Welding (Tungsten Inert Gas) This method is highly favored for welding thin walls of stainless steel due to its precision and control. TIG welding uses a non-consumable tungsten electrode to produce the weld, with a separate filler rod added if needed. The process is characterized by clean and aesthetically pleasing welds, making it ideal for applications where appearance matters.
2. MIG Welding (Metal Inert Gas) MIG welding is another common method used for stainless steel. It employs a continuous feed of filler wire and inert gas to shield the weld pool from contamination. Although it is generally faster than TIG welding, it may not achieve the same level of control. MIG is often preferred for thicker materials or when speed is essential.
3. Stick Welding (Shielded Metal Arc Welding) While not as popular for stainless steel pipes, stick welding can still be utilized. It involves the use of a consumable electrode coated in flux, which generates a gas shield during the welding process. Stick welding is typically more forgiving in outdoor environments but may leave slag that needs to be cleaned.
stainless pipe welding
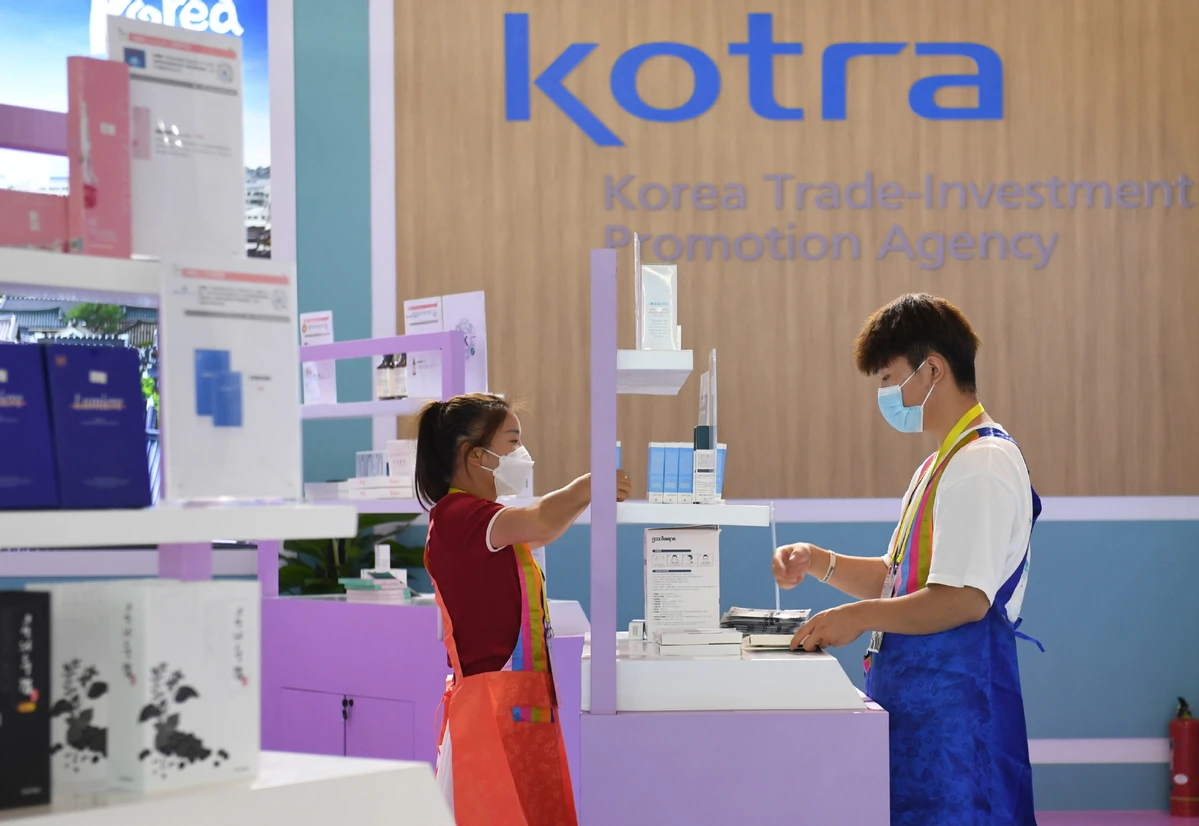
Preparing for Welding
Preparation is key to successful stainless pipe welding. The pipes should be thoroughly cleaned to remove contaminants such as oil, grease, rust, and scale. A clean surface ensures a better bond and reduces the risk of weld failures. Additionally, proper fit-up and alignment of pipes are crucial to avoid distortion during the welding process.
Welding Filler Materials
Selecting the appropriate filler material is another vital component of welding stainless steel pipes. Filler rods or wires should ideally match the base metal grade to prevent issues such as corrosion at the weld joint. Common filler materials for stainless steel include ER308 for 304 stainless steel and ER316 for 316 stainless steel. The choice of filler material affects both the mechanical properties of the weld and its resistance to corrosion.
Post-Welding Treatment
After welding, it may be necessary to perform post-weld treatments such as passivation or pickling. These processes help remove oxide layers and restore the stainless steel's protective chromium oxide layer. They also improve corrosion resistance and enhance the appearance of the welded area.
Safety Considerations
Safety should always be a priority during the welding process. Protective gear including gloves, helmets with appropriate filters, and protective clothing is essential to shield against sparks, UV radiation, and harmful fumes. Adequate ventilation is also crucial in preventing the buildup of hazardous gases.
Conclusion
Welding stainless steel pipes involves understanding the material's properties, selecting the right technique, and ensuring proper preparation and post-weld treatment. Mastering these elements can lead to strong, durable, and corrosion-resistant welds, essential for the reliability of systems in various applications. With advancements in technology and techniques, professionals in the field continue to enhance their skills, ensuring that stainless pipe welding remains a pivotal aspect of modern manufacturing and construction.
Post time: Dec . 23, 2024 14:37